Design and Optimization of Powertrain Components
Ever-increasing environmental regulations, as well as strong competition in the market, demand a very high level of performance in current powertrain design, with typical goals such as reducing fuel consumption and emissions. Modern CFD solvers for reactive and non-reactive flows allow the designers a good insight into the performance measures of interest, but can be challenging and time-consuming to employ on a wider scale, especially when performing parameter studies. A proven way to overcome these challenges is automated design exploration and optimization.
Optimization and automated design exploration augment the development process by leading to better and optimized designs, shortening development times and reducing design cycles, as well as increasing the knowledge about the product’s behavior, i.e., the influence of various parameters on its performance, early in the design process, when the freedom for making decisions is largest.
Apart from the aforementioned simulation tools, two crucial components are needed to achieve the desired process automation: a driver of the optimization process with appropriate systematic variation and optimization strategies, and a suitable CAD tool that can reliably produce the different geometry variants that should be analyzed.
CAESES® is a comprehensive software solution for exploring and optimizing complex powertrain components. CAESES bridges the gap between traditional CAD and simulation. It provides intelligent geometry models for robust variation of the shape, and CFD automation to conduct design explorations and optimization. In particular, the focus of CAESES is the CFD-ready and variable CAD.
Why Would I Need an Additional CAD System?
In our experience, the primary bottleneck in setting up and running an automated design exploration or optimization process is related to the handling of geometry:
- Geometry variation with traditional CAD systems is often tedious or prone to failure, i.e., some or even many of the variants fail to regenerate when changing parameter values.
- It is difficult to consider, or even automatically fulfill, given constraints.
- Simulation engineers depend on the CAD department to provide geometry (variants).
- The quality of the CAD model might not be suitable for simulation (e.g. w.r.t. watertightness, level of detail).
For the most part, CAESES® is a highly specialized CAD system that specifically tackles these problems. It is focused on parametric modeling and variation of complex geometries for design studies and optimization. It provides efficient parameterization methods that offer a high degree of flexibility while using less parameters, comprehensive capabilities for integrating constraints, and simulation-ready exports that require no manual processing.
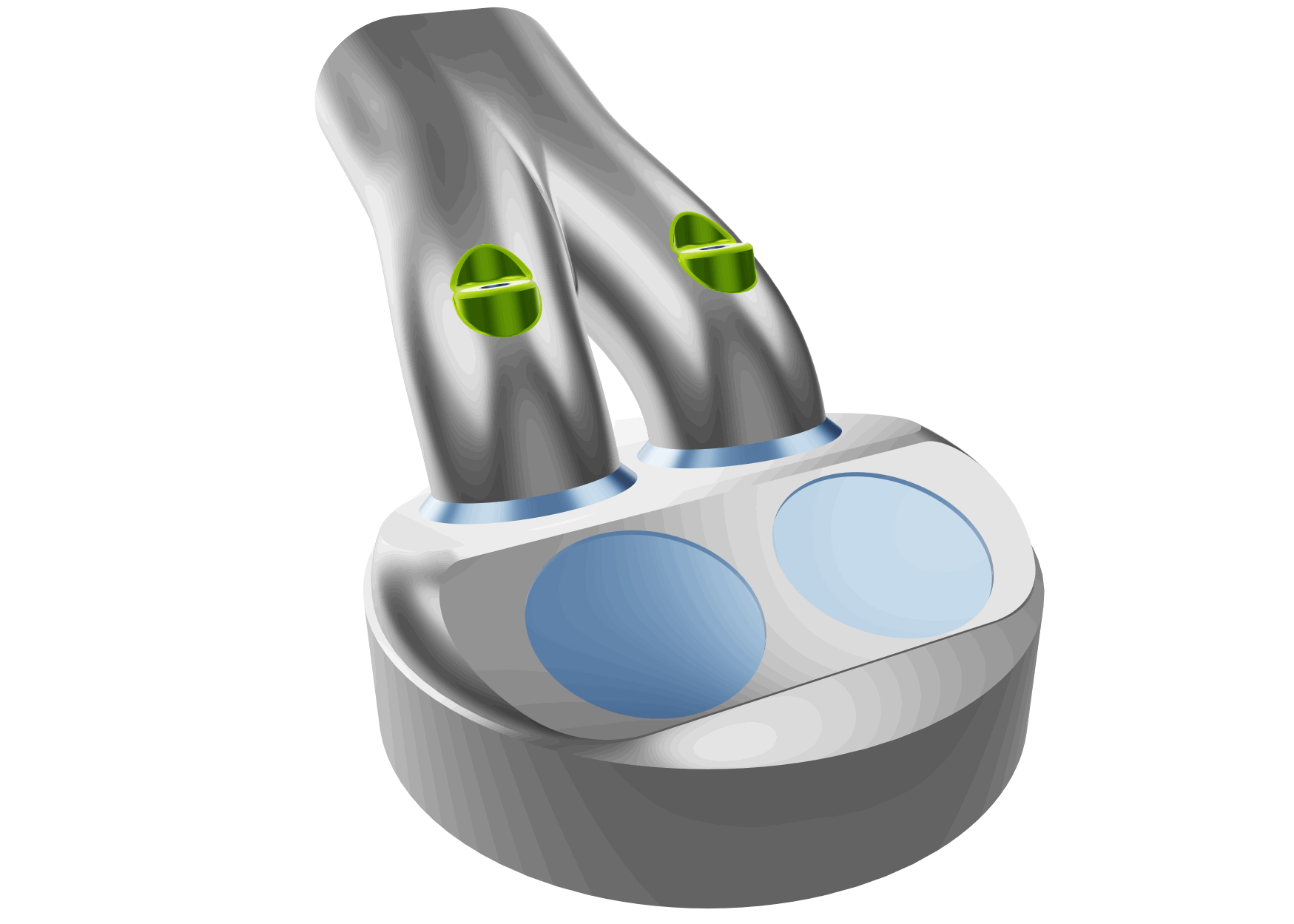
Powertrain Design Capabilities
CAESES® comes with an extensive set of capabilities to support the design and optimization of powertrain components:
- Comprehensive parametric modeling of arbitrary geometries based on fully user-defined parameterizations, with a special focus on complex – often free-formed – geometries that are typically difficult to parameterize in traditional CAD systems.
- Alternatively, flexible and powerful morphing capabilities for quick but controlled modification of imported geometries (discrete or NURBS based).
- Robust variation with little to no failed variants.
- Full consideration of constraints, e.g., due to manufacturing and packaging reasons.
- Geometry exports in several different formats suitable for your CFD/meshing tools. Most of the formats support patch naming, so that downstream tools can correctly identify surface patches for the assignment of individual mesh settings or boundary conditions.
- Generic interface to easily connect CAESES® to external solvers (typically CFD, but also structural and other disciplines).
- Fully-featured optimization environment with a wide selection of DoE and optimization strategies, as well as data management and post-processing capabilities.
- Full scriptability, to easily integrate CAESES® in third-party optimizers like modeFRONTIER, Optimus, optiSLang, and more.
Powertrain Applications
Typical applications for CAESES® in powertrain design are:
- Intake and exhaust ports
- Piston bowls
- Intake and exhaust manifolds
- EGR systems
- Turbochargers
- Fuel injectors and delivery systems
- Exhaust after-treatment, catalytic converters, mufflers
- Water and oil pumps
- Engine coolant jackets
- Electric powertrain components, especially w.r.t. battery, electronics and motor cooling
Who Uses CAESES?
Leading players in the powertrain sector, such as automotive OEMs, Tier 1 suppliers, heavy duty engine manufacturers, research organizations, and engineering consultants use CAESES® for the optimization of powertrain components. This includes companies like VW, MAN, Cummins, BMC Power, BRP, Aramco, Garret Motion, and ZF.
Case Studies and Blog Posts for Powertrain Applications
Questions ?
Please do not hesitate to get in touch with us if you have questions in the context of your specific application. We look forward to discussing it together with you!