Ship Hull Design
Design ships with better flows! CAESES® enables you to build robust parametric ship models with smarter shape control. It is the leading software solution for naval architects that are interested in CFD-based hull optimization – to create better flows around their designed vessels.
The focus of CAESES® is on the underwater part of the ship:
Create a variable hull model, connect your CFD and run studies. Finally pick an optimized hull shape that outperforms similar ships in the market.
Massively Save Costs and Resources
Why using CAESES®? Consider a 14.000 TEU container vessel that runs with IFO380 fuel: By optimizing the vessel’s hull form with CAESES® to gain a 4-5% improved efficiency, the ship operator can save more than 1.000.000$ of fuel costs – per year! At the same time, this helps saving our planet by massively reducing NOx, SOx and CO2 emissions.
CAESES® beneficiaries can save more than 1.000.000$ of fuel costs – pear year!
Create Smarter Variable Models from Scratch
So how to start with the vessel optimization? First, set up a smart variable geometry while at the same time you build-in all your design constraints (displacement, center of buoyancy, hard points etc.). Save time by only generating feasible designs – manually or fully automated by using the intuitive variant management system of CAESES®.
Any Type of Vessel
No matter which kinds of ship hull forms you need to design and optimize – CAESES® is a generalized hull modeler for any type of vessel!
Fast Optimization of Existing Ship Hulls
If your time frame is short and you have no time for creating a whole model, you can use the efficient Lackenby shift transformations and other deformation methods of CAESES®. These transformations allow you to intuitively reshape your hull, again manually or automated in an optimization. Works with any imported geometry!
Hydrostatic Calculation
In an easy-to-use and intuitive way, CAESES® provides you the most important hydrostatic quantities such as displacement and moments of inertia etc. These values can be calculated manually for a new design, or fully automated for a set of design candidates.
Leverage your Flow Analysis Tools
CAESES® closely integrates with your CFD and CAE analysis tools – no matter which CAE package you use. There is also an add-on for the CFD code SHIPFLOW, the industry standard for shipbuilding. Connect typical analyses to your CAESES® model such as ship hull hydrodynamics, wave resistance, and wake field analyses, involve motion analyses of vessels and platforms with seakeeping codes, as well as propeller performance with CFD.
Automation of Pre-Processing
By means of feature definitions, CAESES® gives you a flexible and powerful environment to automate anything, including tedious pre-processing tasks such as the creation of clean surface meshes. See the article “CFD Flow Domain for Ship Hulls from NAPA IGES Files” for an example. It describes the single-click solution for generating a closed flow domain from unclean NAPA IGES files.
Template Models
As a new development (still in a beta phase), CAESES® hull design setups can be fully wrapped into an easy-to-use interface, including meshing, CFD analysis and even optimization runs. Based on the tools that you use in your company. Just change the hull’s main dimensions and other project-specific key parameters and let CAESES® do the number-crunching job of finding the optimal design candidate. Here is a short video that demonstrates how templates can be used from within a browser (see also the blog post about the SMM competition).
Propeller Design
CAESES® allows you to create any type of marine propeller blades. It generally focuses on the advanced design of highly customized and optimized propellers. Point data can be automatically imported and interpolated or parameterized, and complex Excel sheets can be accessed or even completely transferred to the CAESES® environment. CAESES® comes with a set of NACA profiles, but sections can also be defined by yourself using the CAESES® feature programming language. There are also complete parametric propeller setups based on standard series (e.g. Wageningen – see this blog post).
CAESES® gives you everything you need to model typical marine propellers and special types such as surface-piercing or racing propellers, high-skew propellers, ducted propellers and submarine propellers. The propeller add-on gets used by large companies such as ThyssenKrupp Marine Systems and Caterpillar.
Propeller Solids
CAESES® is also able to create a solid propeller geometry from PFF files. Don’t waste time anymore with remodeling a propeller using traditional CAD systems. Just provide this simple ASCII file with your sectional data and generate a full propeller model including tip and hub – all with a single click, it just takes a few seconds. Such a model is ready for being manufactured but also for further studies such as CFD and stress analysis.
Tip and Fillet Modeling
There is dedicated functionality to close propeller tips with a smooth surface. For the fillet creation between the hub and the blade, you can choose between radii-based and variable-radii fillet surfaces. These fillets can also be varied and optimized automatically, if needed.
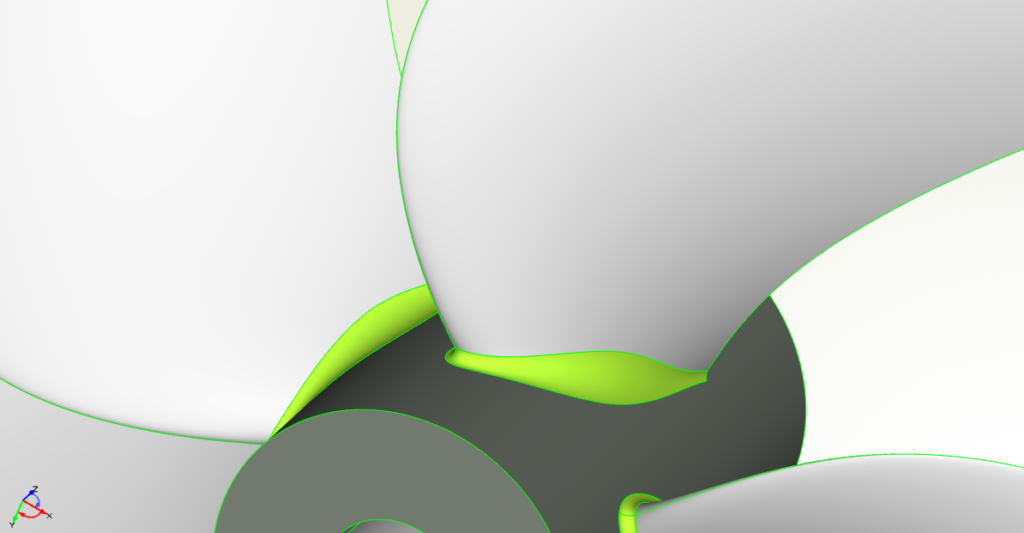
Choose between constant-radius fillets or define variable-radii fillets between the hub and the blade surface
Propeller Boss Cap Fins
CAESES® allows you to design and optimize all sorts of energy-saving devices such as propeller boss cap fins.
Marine Example Applications
- Parametric ship design incl. hydrostatic calculation
- Hull form optimization (container carriers, offshore supply vessels, tankers, yachts, racing boats etc.)
- Propeller design
- Appendages and energy saving devices
- Design and placement of thrusters
Downloads
Please find a summary of the CAESES® design capabilities for marine applications in this brochure (PDF). There is also a short tech brief (PDF) about the most relevant features and benefits for ship hull form design in CAESES®.
More Information
At FRIENDSHIP SYSTEMS our heritage is in the Shipbuilding & Marine sector, and we count many of the largest shipbuilders in the world as our customers. We have best-in-class expertise in parametric modeling of hull forms, appendages, propellers, etc. In order to drive the innovation of our products, FRIENDSHIP SYSTEMS has always been involved in challenging research projects for ship design and optimization.
References
CAESES® is used by all leading ship design offices and ship yards in the world, such as Daewoo Shipbuilding & Marine Engineering (DSME), Hyundai Heavy Industries, Samsung Heavy Industries, Kawasaki Heavy Industries, Shanghai Merchant Ship Design & Research Institute (SDARI), CSSC. In Germany, e.g. HSVA, TKMS, Meyer and Neptun Ship Design are using CAESES®.
Further Interesting Articles and Videos
Here is a short read about a twin skeg study, and another blog post with a video about skeg modeling in 2 minutes. CAESES® can also be used to design and optimize very special ship hull components such as spudcans (the “feet” of the jacking legs). Interested in saving the planet? Read more about annual CO2 reductions by CAESES®.
Please don’t hesitate to get in touch with us if you are interested in using CAESES® for your specific marine application.