Optimization of a Volute and a Vaned Diffusor of a Centrifugal Compressor
An automated and simultaneous optimization of a vaned diffusor and volute of a centrifugal compressor was studied in this project at TU Darmstadt (Institute of Gas Turbines and Aerospace Propulsion). The study was done in cooperation with NUMECA Germany and Kompressorenbau Bannewitz (KBB).
For the automated generation of geometry, CAESES® came into play, while NUMECA products were used for the meshing and CFD part. In CAESES®, the shape of the volute’s cross sections as well as the area distribution of the volute got varied. The non-axissymmetric parameterization of the diffusor allowed for quick changes to the blade, by modifying the stagger angle, blade twist, chord length, pitch and rotation.
The isentropic efficiency, which was used as objective for the optimization, could be calculated by means of a CFD simulation of the whole compressor stage (impeller, diffusor and volute).
Key Benefits
Within this project, all partners gained a lot of new insights and further knowledge regarding the design and optimization of centrifugal compressors. The main benefits can be summarized as follows:
- Fully-automated optimization of diffusor and volute
- Big impact of diffusor, additional impact of volute
- Increase of isentropic efficiency by 1-4%
- Increase of total pressure by 1.45-4.67%
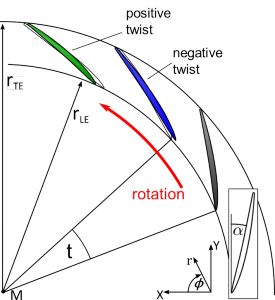
Variation of Diffusor Blades
“With CAESES® we could build an upfront CAD model for a compressor that gave us top-quality shapes with very few parameters. This allows us to simultaneously optimize the geometry of the diffusor and the volute with respect to isentropic efficiency. In our opinion the parametric approach taken within CAESES® is ideal for the modeling of turbomachinery components.”
— Johannes Ratz, Research Scientist, Institute of Gas Turbines and Aerospace Propulsion, Technical University Darmstadt
More Information