Drone Propeller Design and Shape Optimization at Parrot
The French company Parrot SA uses CAESES® as a customized design framework for drone propellers. Being one of the leading companies in the drone market, the engineers’ motivation for introducing CAESES® came from the goals of speeding up their design process and delivering optimal products.
Process Automation and Innovation
One of the objectives for the new design process was the comprehensive automation of several tedious and time-consuming manual design tasks, such as importing profile (airfoil) data, fitting parametric models, 3D surface creation, geometry clean-up, controlling the meshing process etc.
Another driver was innovation: The new framework should allow them to set up and explore innovative new blade concepts in an automated way, and much faster than with traditional iterative workflows. For this purpose, the new process includes a flexible geometry parameterization that provides comprehensive shape control, as well as specific features for design experiments and studies. This setup allows the engineers to generate a blade design from scratch, to try out completely new ideas, and to robustly automate the creation of new design candidates for subsequent CFD analysis. Everything should be as convenient and automated as possible, starting from importing airfoil data up to the meshing and analysis procedure with 3rd party tools.
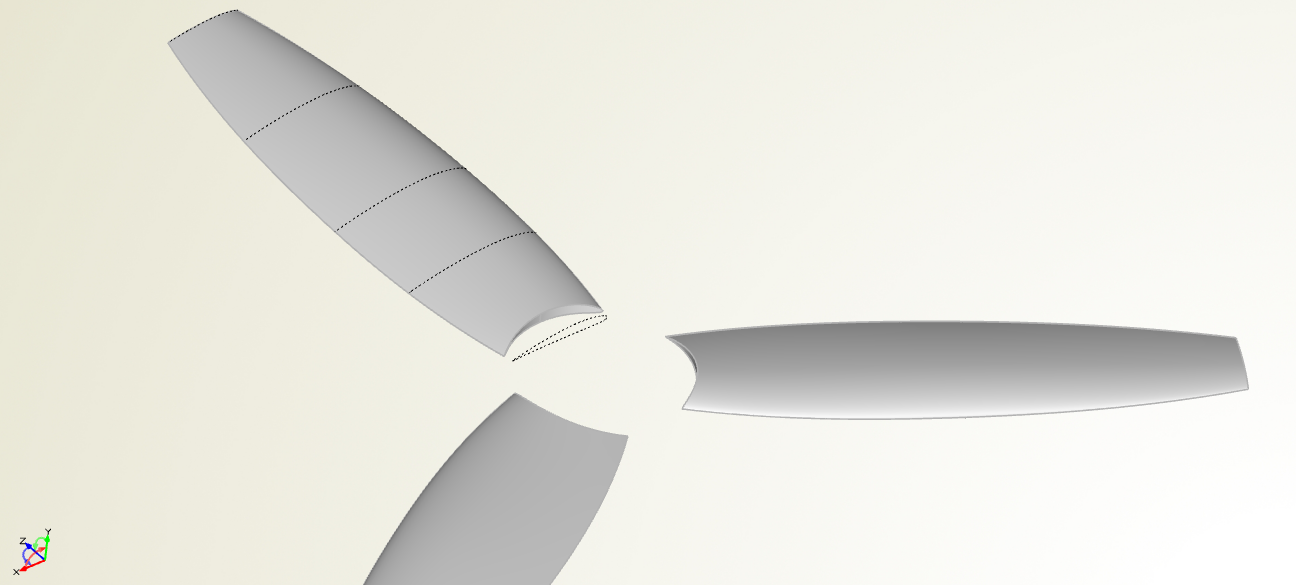
Parametric drone propeller in CAESES, to create simulation-ready models for automated studies with CFD tools
The New Propeller Design Framework
Based on the requirements from the Parrot engineers, a flexible new framework was implemented within a couple of weeks. The following blade design tasks are now fully automated, to create a geometry with just a few clicks:
- Import 2D airfoil data for different radial positions, interpolate these point data with 2D curves and visualize important quantities
- Modify key profile parameters such as camber and thickness
- Import radial distributions for typical controls such as chord, rake, skew, pitch that are generated by a preliminary design tool
- Fit parametric distributions with design variables to these imported distributions (optional)
- Provide further parametric capabilities for exploring innovative designs on-the-fly
- Create a solid and clean 3D blade surface with fixed patch IDs that can be readily meshed
- Allow users the automated meshing of such a new design
- Allow users to run automated design studies and shape optimization using the design variables of the framework
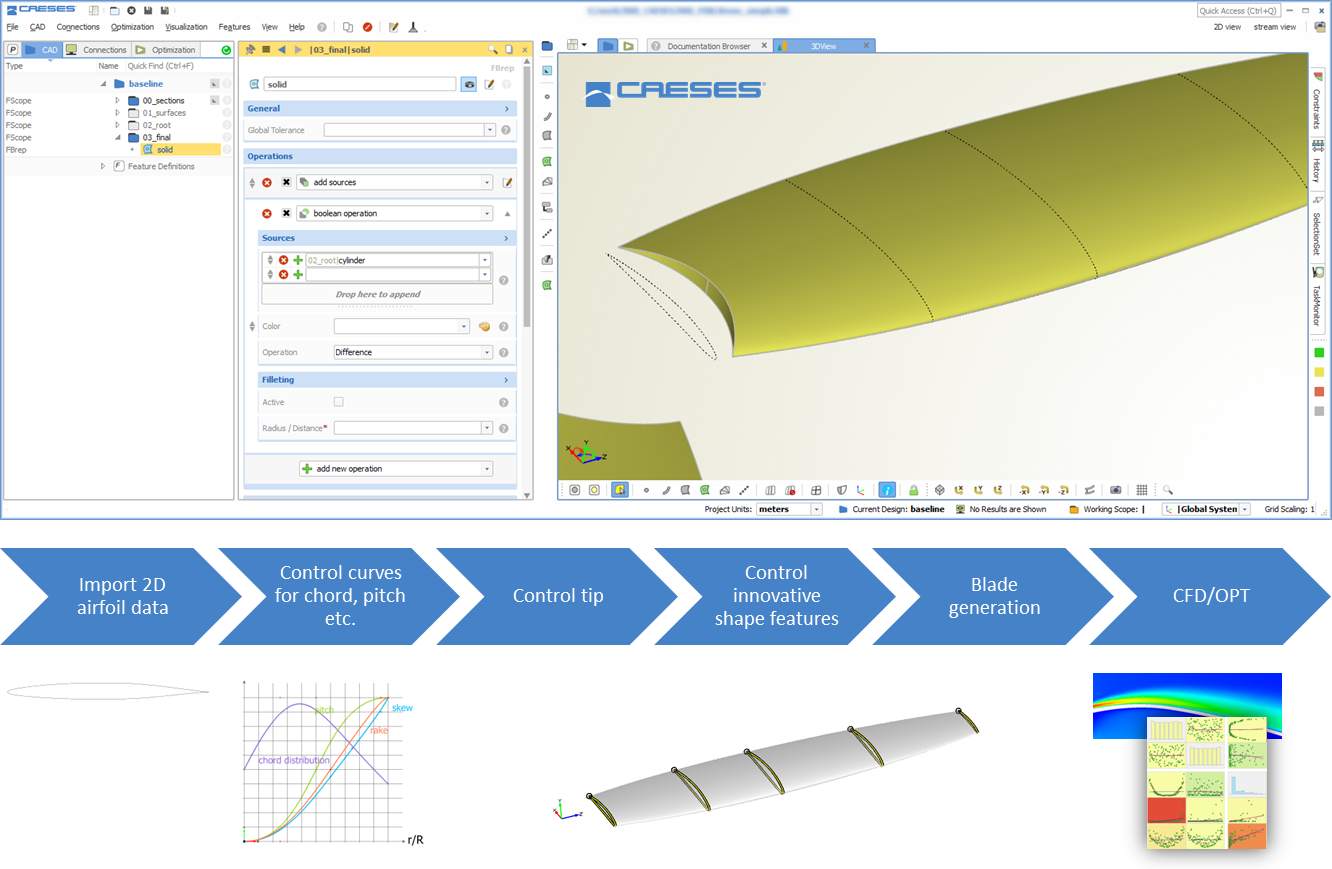
Automated in CAESES: From importing airfoil data up to 3D blade creation and shape optimization with simulation
“The implementation of the design workflow based on CAESES has drastically reduced the development time of propellers from months to days, by giving us the possibility of generating hundreds of blade geometries in just a few minutes. Also, CAESES is seamlessly integrated into the ANSYS CFD optimization process, which allows us to perform automated high-fidelity parametric studies. The design freedoms obtained by introducing CAESES let us explore new limits in propeller design.”
— David Gomez Ariza, Aerodynamics and Propulsion Expert, Parrot
Automation through Features
The tasks and process automation described above can be realized using the feature definition capabilities of CAESES®. Instead of doing each step manually in the GUI of CAESES®, most of these tasks can be scripted and automated within the intuitive CAESES® feature programming environment.
All feature definitions can be accessed and modified by Parrot, to make sure that they can still apply changes and extensions at a later stage. The environment allows users to create functions and command sequences, as well as comments to document everything. Within such a feature, one can e.g. create curves from point data, apply a fitting procedure and visualize labels in the 3D view. The imported airfoils can also be automatically analyzed with regards to quantities such as maximum thickness and camber information.
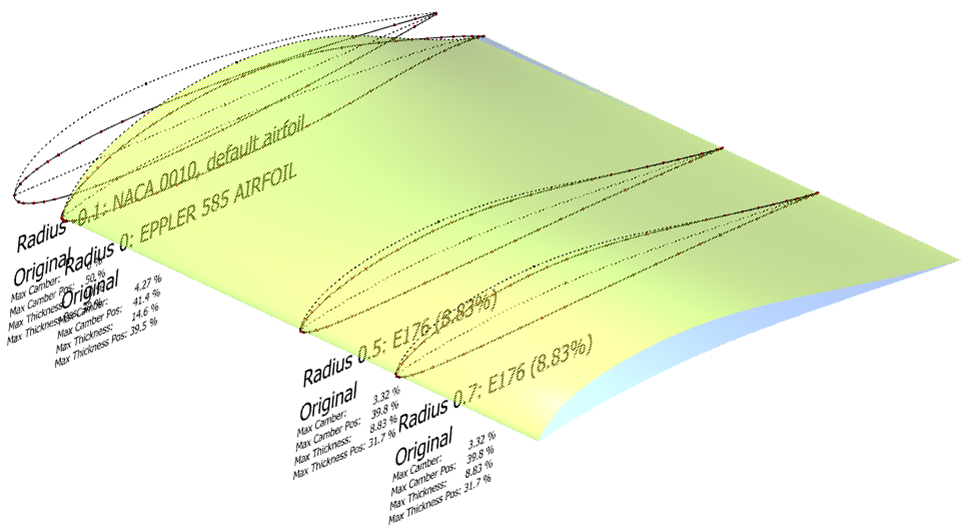
Feature Programming: Import 2D airfoil data for drone blades, analyze and visualize all required information automatically
CAESES App for Integration in ANSYS Workbench
As a follow-up work, Parrot and FRIENDSHIP SYSTEMS (the makers of CAESES®) are now tackling the realization of a so-called ACT app that allows the engineers to use this new drone blade design framework directly within the ANSYS Workbench. Through this new app, geometry variants can be created directly within the ANSYS Workbench using the ANSYS Parameter Set, without switching to the CAESES® GUI. By using an additional external meshing software, the final meshed geometry is transferred to the ANSYS Workbench for simulation. Since this is an automated process, Parrot can run design studies and shape optimization with this app, using either the integrated optimization methods of the ANSYS DesignXplorer or tools such as optiSLang.
More information about the CAESES® and ANSYS ACT apps can be found in the article “Shape Optimization in ANSYS with CAESES”.
More Information
See the CAESES® product pages for more information. Interested in parametric drone blade design and shape optimization with CFD (Computational Fluid Dynamics)? Or any questions regarding this case study? Feel free to get in touch with us! If you want to read more about drone blade design, see also this blog post. If you like to receive news like this directly to your inbox, then subscribe to our newsletter.