This academic blog post describes how CAESES was used to design a parametric turbopump inducer geometry in conjunction with Ansys CFX.
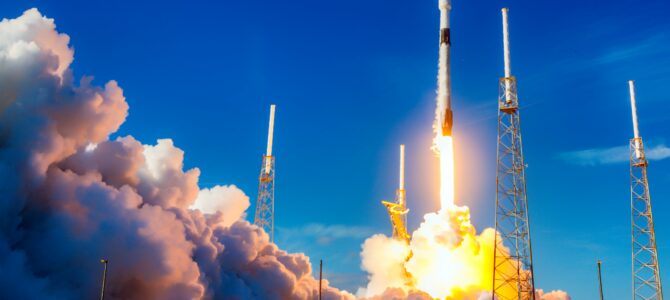
This academic blog post describes how CAESES was used to design a parametric turbopump inducer geometry in conjunction with Ansys CFX.
This blog post deals with the improvement of the design of the internal layout of oil tankers targeting safety and economic feedback and considering the incorporated uncertainty.
The present work explores novel sCO2 axial turbine designs for waste heat recovery (WHR) applications based on a 10 MW case study. A Kulfan Class Shape Transformation (CST) for 2D axial blade profile design is employed, and considerations are undertaken for aerodynamic efficiency and mechanical stresses.
There is no excerpt because this is a protected post.
The main goal of this study is to enhance hydro-acoustics and hydrodynamics performance of a submarine hull with bow form optimization using high-fidelity CFD simulations and an automated workflow.
Predicting the transitional boundary layer is still an almost impossible task for arbitrary flow conditions. The consideration of the impact of boundary conditions such as pressure gradient, free-stream turbulence and surface roughness demand improved transition models, which are the interest of a research group at the Karlsruhe University for Applied Sciences. CAESES was introduced as the process integration and design optimization (PIDO) platform to optimize the leading edge contour.
The aerodynamic optimization of bicycle wheels can lead to decisive gains in running pace. Nowadays, aerodynamic performance is one of the key factors considered when racing cyclists purchase new equipment. The aim of this project was to investigate the aerodynamics involved in bicycle wheel design, and to optimize and design a very low drag bicycle wheel rim shape using CAESES & TCFD.
The design and optimization of valves is one of many applications where using CAESES® to robustly automate the processes of systematic geometry variation and analysis of the generated variants with a suitable CFD solver can lead to significant reductions in time-to-market, as well as to a truly optimal design within the specified constraints.
The CAESES ACT app is an ANSYS geometry interface by FRIENDSHIP SYSTEMS that allows CFD engineers to automate the entire geometry generation process, for the purpose of running shape optimization and design studies.
The design of axial fans typically considers the efficiency but also the reduction of the noise emissions. Axial fan noise reduction is a rather huge and complex topic when it comes to all the details, but there are a few simple CAD techniques that you can apply to your standard blade designs, to immediately enhance the fan’s noise level.