This blog post is part of our CAESES Student Award 2020 competition about the use of CAESES in academia, where we showcase exciting material submitted to us by students who use CAESES in their research. Many students from high school to PhD make use of CAESES to reach their project goals. If you are one of them, we encourage you to send us an article about your project and how CAESES has helped you. Interesting articles will be posted regularly in our blog, along with some information about the author, and at the end of February 2021, we will select the best author, who will win some exciting prizes.
Introduction
The size and location of the internal spaces are established in the early stage of ship design. For oil tankers, the internal hull layout design can be defined as an optimization problem to improve ship performance during the life cycle. The internal layout of oil tankers can be optimized targeting the improvement of the economic returns and the safety and prevention of environmental pollution. The prominent indicators of these objectives are identified as the cargo capacity, induced bending moment to the ship hull and oil outflow performance for a fixed hull shape. This work deals with the improvement of the design of the internal layout of oil tankers, targeting safety and economic feedback and considering the incorporated uncertainty.
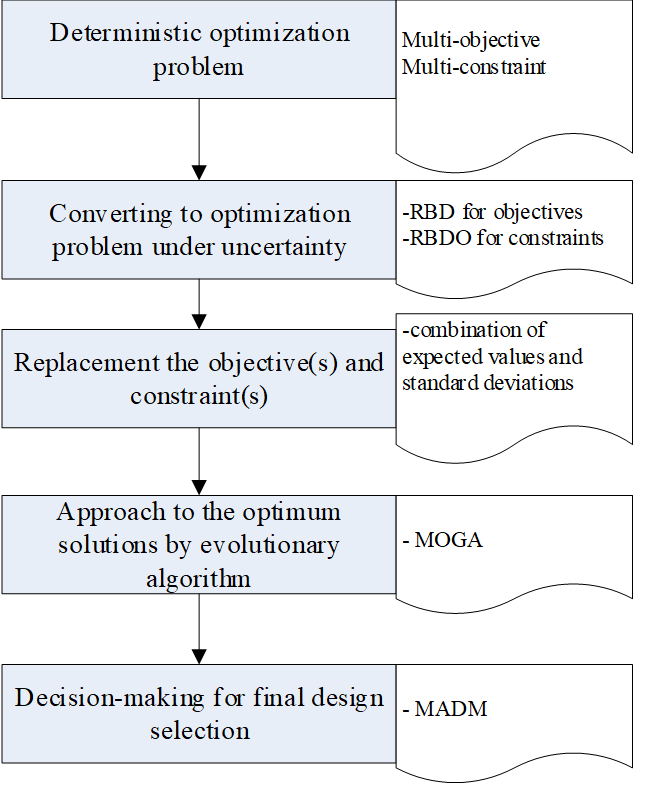
Presentation of the applied process for incorporation of uncertainty into the design problem of hull internal layout
Definition of Optimization Problem
Design Parameters
The ship hull shape is assumed to be fixed. Therefore, the main challenge of the problem is defined by the determination of the dimensions of the internal compartments and tanks to approach the optimum of the interest functions.
Constraints
The majority of constraints are of inequality type due to regulations of SOLAS (2012; International Convention for the Safety of Life at Sea, International Maritime Organization, London, Chapter II) and MARPOL (2006, International Convention for the Prevention of Pollution from Ships, Annex I. International Maritime Organization, London.). However, they can be translated to equality constraints. For instance, intact stability criteria include inequality limitations for transverse and longitudinal stabilities. Eventually, all those constraints can be translated to an equality constraint of intact stability regulations with two options of pass (equal to 1) or not pass (not equal to 1). A combination of the two approaches was applied to constraints to simplify the categorization of the limits. Especially, the approach is helpful during the identification of the priorities for constraint conversion to robust-based approach. To model the uncertainty of oil outflow due to possible damages, the regulatory constraint is replaced by using a 3-sigma formulation. So, a tolerance between is defined for the solutions and the original constraints.
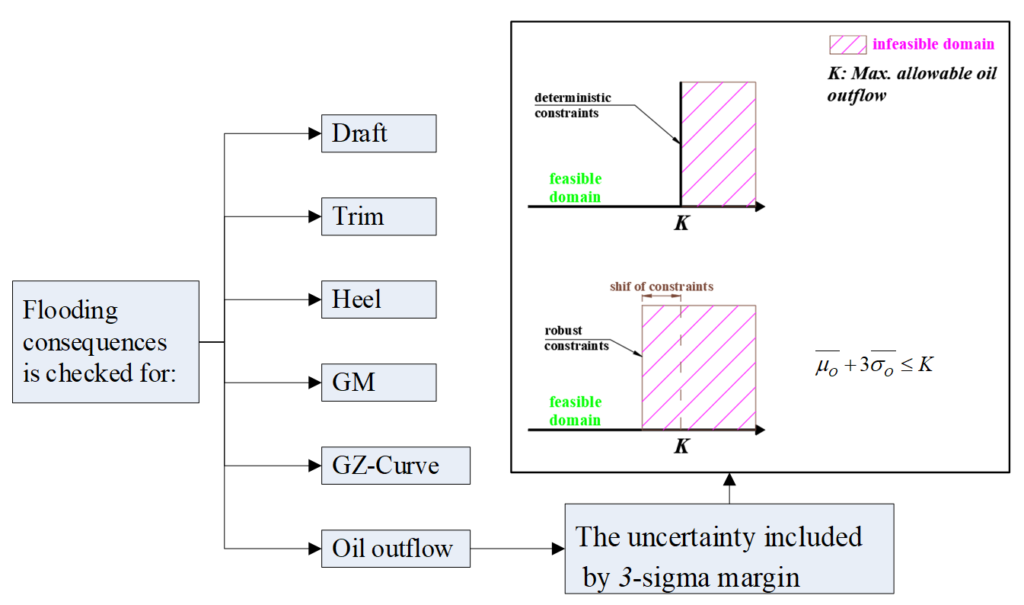
The regulatory constraints are checked for the consequence of flooding with incorporation the uncertainties of the accidents.
Objective Functions
The main aims of the optimization problem are defined by increasing safety and economic functions. Thus, the following objectives are defined for the optimization problem:
- Maximization of the Cargo Capacity
- Minimization of the Maximum Hogging Still Water Bending Moment
- Minimization of the Maximum Sagging Still Water Bending Moment
The maximum still water bending moment (SWBM) is induced to this ship hull in the hogging condition, however, the sagging has a more important effect on the safety and environment protection objectives. This is because the sagging extreme values are in the full load condition, while, the extreme values of hogging are usually happening in the full ballast conditions. Thus, the minimization of maximum sagging and hogging loading was defined as two separate objectives. The uncertainty of SWBM is modelled by normal distributions. The expected values and standard deviations of the distributions of the sagging and hogging are calculated separately. The robust objectives of sagging and hogging are replaced using the 3-sigma method:
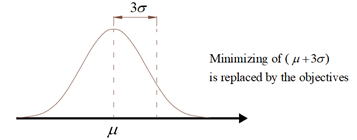
The reduction of mean value and standard deviation of the bending moment results in safer design with lower uncertainties.
Optimization Procedure
The optimization procedure includes:
- updating the model according to the design parameters
- applying the predefined loading conditions and damage scenarios to the model
- performing the intact and damage stability analysis
- updating the uncertainty model
- evaluating the objective and constraints
- checking the criteria
- running the multi-objective genetic algorithm (MOGA) for optimization
- repeating the above stages until reaching the stopping criteria
Results and Discussion
The evolution direction of the obtained solutions can be recognized toward the Pareto solutions, which includes the higher value of cargo capacity and smaller values of maximum sagging SWBM. The reference design is approximately in the middle range of the objectives’ values for the obtained solutions. Globally, plenty of solutions had better values of the mentioned objectives relative to the reference design. Even locally, the reference design can be improved from the aspect of the cargo capacity and maximum hogging and sagging SWBM.
The constraint values are at an acceptable level relative to the allowable oil outflow parameter for the designs. The marginal distance of each design relative to the allowable value is dependent on the uncertainty term. The distance increased for those solutions that have a higher standard deviation of oil outflow.
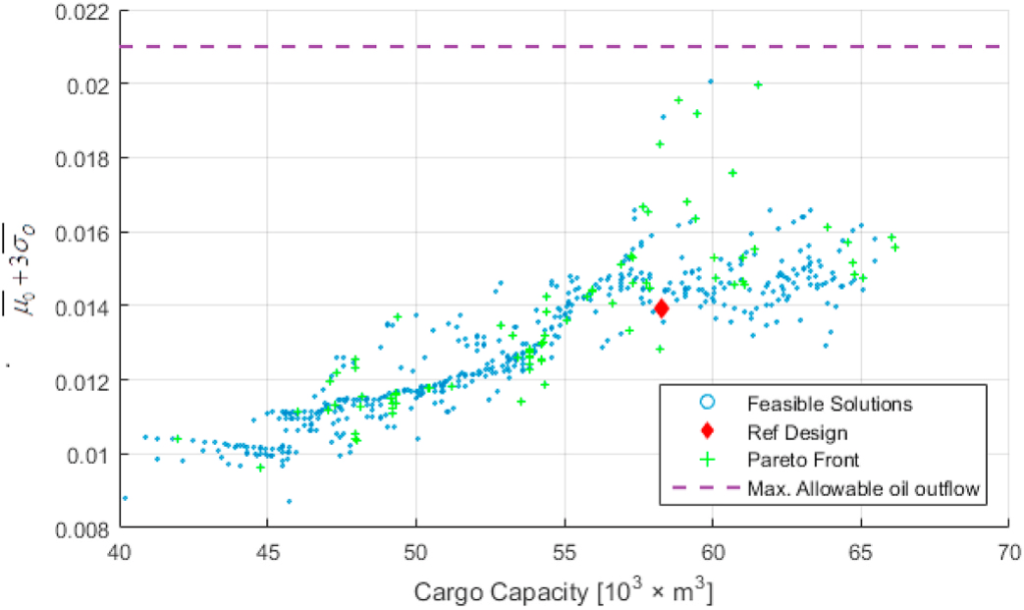
Presentation of the robust constraint against the cargo capacity for the feasible and Pareto solutions
Decision-making for Final Design Selection
The final optimal solution can be selected by a trade-off between conflicting objective functions. Thus, the selection of final designs can be defined as a Multi-Attribute Decision Making (MADM) problem. So, the Pareto solutions can be judged by the MADM methods and the superior design can be identified among the available alternatives. For this purpose, the degree of importance of objectives needs to be specified by assigning a weight to each objective function.
Here, two alternative scenarios are presented:
- alternative 1 is selected by defining equal weight for criteria,
- alternative 2 is defined by dedicating higher importance to the cargo capacity relative to other criteria.
Conclusions
The interest functions are improved for the obtained solutions based on a robust-based method, besides the solutions are limited to the designs that are in the reliable region of criteria limits. The reference design can have a considerable improvement in the induced loads to the ship structure, even if the cargo capacity remains unchanged. The obtained solutions provide a wide range of diversities for the designer to have free hand for design selections.
About the Author
Special thanks to Hamidreza Jafaryeganeh from the Instituto Superior Técnico in Lisboa, Portugal. It is always inspiring to see your enthusiasm and dedication to optimization tasks with the help of CAESES.
Hamidreza is a research assistant at Instituto Superior Técnico. He has experiences in the fields of hydrodynamic simulation, modeling uncertainties, damage stability analysis, optimization of structures and decision-making for design selection. He also benefits from working experiences of the detail and basic design in offshore industries.
“CAESES is a very beneficial tool for facilitating the parametric modeling, simulation-driven design and design optimization. By using CAESES, I focused on the defined objective of my Ph.D. project without any concerns for the technical integration of different modeling and simulation software and optimizing tools.”
– Hamidreza Jafaryeganeh, PhD Student at Instituto Superior Técnico
More Information
The full version of this contribution can be found here.