A piston bowl is a recess in the piston crown primarily used in (direct injection) Diesel engines, where it basically forms the combustion chamber. The design and shape of the piston bowl influences the movement of air and fuel during the compression stroke, thereby affecting the air/fuel mixture. A good mixture leads to a more efficient combustion, resulting in more power or better fuel economy. Additionally, using an effective piston bowl shape can reduce the in-cylinder emissions (like NOx and soot) and the cost for after-treatment.
CAESES’ Piston Bowl Design Capabilities
CAESES® has been effectively used to design state-of-the-art piston bowls and brings along several key capabilities for this specific task. Here is a short summary:
- Arbitrary profile parameterizations can be used. The design of your specific piston bowl is not limited to certain pre-defined templates, but you are free to model your own custom parameterization (or we set it up for you, following your specifications). You want to use linear and circular segments, or rather splines? It doesn’t matter.
- The bowl profile can be varied in circumferential direction, allowing for, e.g., “wavy” bowl shapes.
- Robust variation of the bowl geometry is possible with no failed variants. As for other geometries, one of the most important targets of our software is 100% robust geometry variation, obtained by smart parameterization and dependency-based models.
- The compression ratio can be automatically adjusted for each geometry variant. This is crucial for making sure that every generated variant has the same compression ratio and not wasting time on infeasible designs. It is done with an internal optimization loop, where the variables for the adjustment can be chosen freely. It is even possible to define an order of precedence, so that the automated adjustment first tries to match the compression ratio with the first given variable. If that doesn’t suffice, the next variable is added, and so on.
- Other automated adjustments can be carried out as well, like adjustment of the spray angle in relation to the changing bowl shape.
- The geometry can be exported in several different formats suitable for your CFD/meshing tools. Many of the formats support patch naming, so that the downstream tool can correctly identify surface patches for the assignment of individual mesh settings or boundary conditions.
- A design study on the piston bowl geometry can be combined with an investigation of the injection strategy, or other process parameters (such as fuel composition, EGR amount, etc.). In our Software Connector interface, we can parameterize and modify any value that goes into the input files or scripts for the CFD solver.
Example Case:
Piston Bowl Optimization with CONVERGE
This is a simple optimization study that was carried out to demonstrate the workflow using CAESES® and CONVERGE. The bowl profile consisted of two circular segments, two spline and several linear segments. Four parameters were selected for the optimization:
Lip Entrainment
This parameter controls the size of the lip at the rim of the bowl and thereby the inner diameter of the bowl.
Note that as an option, the area (i.e. volume for a 3D bowl) can be adjusted automatically to meet a given value. This is shown below to give you an example of the dependencies. For the visualization of the remaining parameters of this article, this option is not active so that the single parameter effect is more obvious.
Bowl Radius
This parameter controls the radius of the bottom of the bowl.
Diameter Scaling
This parameter controls the overall diameter of the bowl, by scaling the complete profile in outward direction.
Spray Angle
This is not a geometry parameter, but rather a value that goes into the CONVERGE control files.
CONVERGE was coupled to CAESES® using the Software Connector. A sector of the geometry was cut according to the number of nozzles and exported in a special format for Converge CFD (“surface.dat”), including individual IDs for the identification of the different patches.
The optimization was set up with a multi-objective genetic algorithm that is part of CAESES®. Two concurrent objectives were considered: NOx and soot production. The optimization run comprised about 50 designs and therefore CFD simulations.
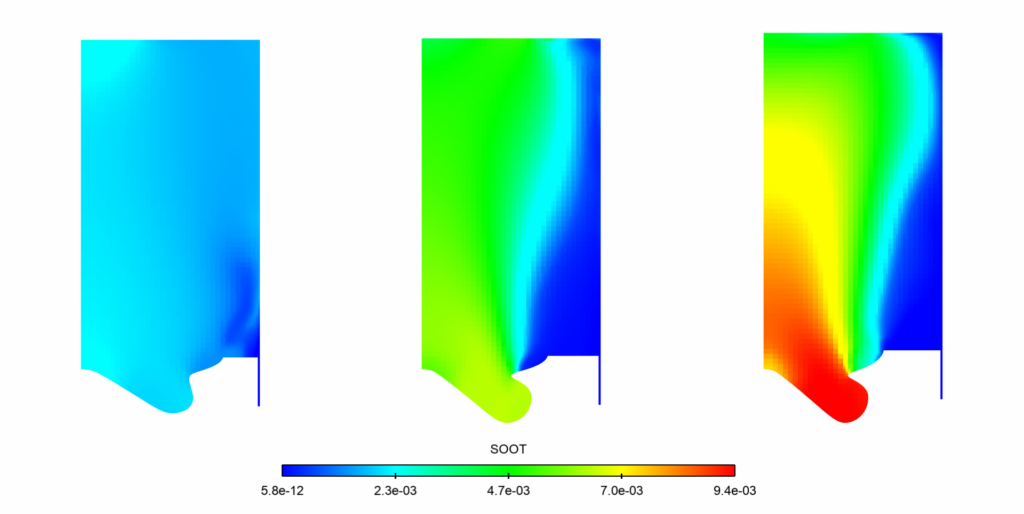
CFD results and visualization of the soot distribution for a selection of different piston bowl candidates
All design variables had a significant effect on the objectives, but the two objectives were – not very surprisingly – anti-correlated. Three designs were chosen from the resulting, still rather sparse, Pareto frontier: the one with the lowest soot, the one with the lowest NOx and a compromise from the middle of the frontier. The baseline was already pretty good in terms of soot, so, while big improvements were possible in terms of NOx production, only the design with the lowest soot could improve upon the baseline.
Fortunately, that design also had lower NOx emissions so that an overall improvement would have been be possible by selecting this design. Possibly, further improvements could have been found by running an additional optimization step, refining the search in the area around the best design so far.
Download Tech Brief
A short summary of the CAESES® piston bowl design capabilities can be found in this tech brief (PDF).
More Information
If you want to hear this story in more detail, you can check out the recording of the webinar we ran jointly with Convergent Science. If you want to get a first impression of a parametric piston bowl created in CAESES®, try the piston bowl web app. There is another related article about piston bowl design which shows a basic parameterization, and a short case study from VW. If you would like to discuss your piston bowl applications with us, do not hesitate to get in touch! Finally, check out the automotive industry section for similar applications.
Follow Us
If you are interested in CAESES and in CFD-driven design optimization, then sign up for our newsletter. Don’t worry, we won’t bother you with too many emails. Of course, you can unsubscribe at any time 🙂
Pingback: Piston Bowl Design › CAESES
Pingback: CONVERGE CFD Software: Full Automation with CAESES › CAESES
Hello,
Wanted to if in order to predict emissions from combustion phenomena was a run for complete intake to compression stroke is required or we can initiate an initial boundary in the combustion bowl with inputs of pressure and temperature of air in the bowl volume?
Hi Gopal,
as far as I know, this was a full cycle simulation. However, the CFD part was taken care of by our partner Convergent Science. You might want to get in contact with them to discuss these issues.