Shape Optimization in the Aerospace Sector
When thinking about e.g. aerodynamic design in the aerospace sector, airplanes, helicopters, and rockets are what first come to mind. However, in aerospace applications there are so many complex geometries around with plenty of details and constraints that need to be considered. CAESES® is an ideal CAD and automation platform for creating, varying, and optimizing these flow-exposed geometries.
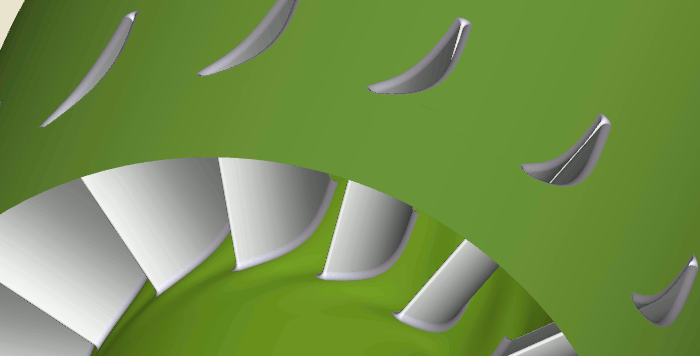
Stator optimization with endwall contouring: Robust variation of several geometry parameters in CAESES
Use CAESES® as your flexible CAD tool for creating aerodynamic geometry. CAESES® comes with a great graphical user interface, but it can also be fully scripted to run in batch mode (e.g. control it with your optimization tool of choice). If needed, you can connect your CFD tools to CAESES® and run studies or shape optimizations right away by using the embedded optimization methods.
The parametric design of 2D sections and the smooth & effective 3D surface generation is a core competence of CAESES®.
Rotor Blades
Create your smarter and variable CAD blade model in CAESES®. However, instead of just sweeping your 2D section design, you have full control in spanwise direction while generating the 3D surface. Define your own parameter distributions for the section parameters and decide what to vary. For section definition, use mathematical expressions, inbuilt NACA curves, NURBS curves or one of the various other CAESES® curve types to explore new designs. Custom profile data can be imported or written into a file by using the feature language of CAESES®, which allows you to define and make use of your proprietary file formats. All design parameters can be addressed and varied by the CAESES® design engines or your external optimization tools. CAESES® is your perfect choice for blade shape optimization with CFD and other tools.
Check out this short blog post about drone blade design in the context of aerodynamic optimization.
LIVE PREVIEW
Check out the online drone blade demo model. Change the parameters and download an example STL geometry. Note that this is a rather simple geometry for quick demonstration purposes.
Profile Fitting
CAESES® can import your discrete profile and blade data, and fit it into your existing parametric CAESES® model. Fully automated, and with just a few clicks. All the geometry models can be set up such that they are ready for analysis, i.e. typically they include the periodic boundaries for meshing and CFD. If you are interested in such a custom fitting procedure or a CFD-ready model, just get in touch with us so that we can discuss it in more detail.
Example Applications
- External flow-exposed surfaces such as wings and appendages
- Engine installation, intake and exhaust ducts
- Aeroengine turbines and compressors
- Airplane propellers and rotors
- Helicopter rotors
- Auxiliary ducts and nozzles
More Information
If you are into shape optimization of aerodynamic components and you think that CAESES® could be helpful for your design work, then just get in touch with us. We’ll get back to you to discuss your application. Note that as an option we can also assist you in setting up a robust and variable model. This gives you a fast start with CAESES®, and lets you readily focus on your engineering task.
Further Reading
Check out the article about stator optimization where a more complex parametric model was created and used for a benchmark. There is also an axial compressor case study from Rolls-Royce where we created custom parametric models in the context of aeroengines. If you are interested in profile fitting, then check out the SIEMENS case study where the starting point in the design process was profile point data.