On January 1, 2023, the Energy Efficiency Existing Ship Index (EEXI) and Carbon Intensity Indicator (CII) will come into force, creating new challenges for operators of commercial vessels. Ship owners and managers must prepare for these requirements by assessing and improving their vessels as needed. This is crucial in order to earn the proper certificates, allowing them to continue sailing and trading internationally.
EEXI and CII
These new mandatory measures have been introduced by the International Maritime Organization (IMO) to cut the carbon intensity of international shipping, setting shipping on a course to meet greenhouse gas reduction targets established in the 2018 Initial IMO Strategy for Reducing GHG Emissions from Ships.
The EEXI is a technical index that determines a vessel’s energy efficiency purely on the basis of the ship’s design parameters. It has to be calculated one time for the initial certification and is based on the same methodology as the Energy Efficiency Design Index (EEDI) for newbuilds. In a simplified way, the EEXI estimates CO2 emissions per transport work (grams of CO2 per ton-mile). Emissions are computed from the installed power of the main engine, fuel oil consumption, and a conversion factor between fuel and the corresponding CO2 mass. Possible reduction factors and energy-saving equipment are considered.
The CII is a recurring operational requirement, calculated as the ratio of the total mass of CO2 emitted (from actually consumed fuel) to the total transport work (from the distance traveled and the ship’s capacity) in a given calendar year. A vessel’s annual carbon intensity performance will be compared against the IMO’s rating system which categorizes ships into A, B, C, D and E. Vessels which receive a D rating for three consecutive years or an E rating for one year are required to submit a corrective action plan to demonstrate ways in which they will improve their performance.

Several options for technical and operational improvements are available for ships that must moderately or significantly minimize emissions and improve fuel consumption. These include switching to low-carbon fuels, limiting engine power, reducing speed, and retrofitting vessels with energy-efficient technology.
Corrective Measure and Hydrodynamic Optimization
One subset of the corrective measures that can be taken to achieve EEXI and CII compliance is related to improving the hydrodynamic performance of the ship by means of different retrofits. These measures have in common that their effect is to either reduce the required power and therefore fuel consumption, or alternatively, to increase the vessel’s speed for a given power, as both cases will equally lead to an improvement of the indexes. Sometimes, they make sense in combination with other measures, e.g., in the case of a poorly performing bulbous bow for a ship that is operated at a significantly reduced speed. Typical examples for retrofits are: bulbous bow replacement, propeller modification, air lubrication systems, wind assisted propulsion systems, and energy saving devices like wake ducts, pre-swirl stators and propeller boss cap fins.
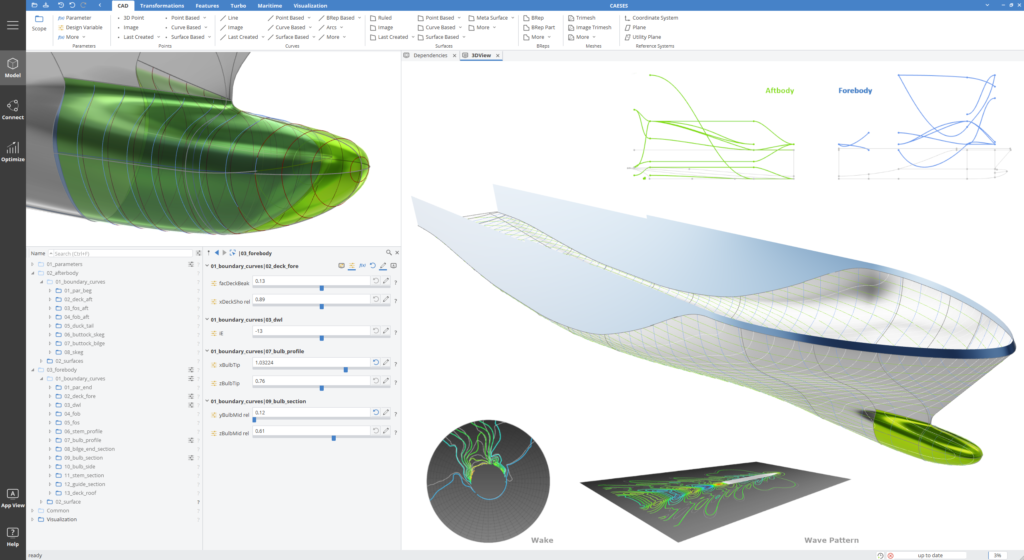
As most of these retrofitting measures require serious investment, it is crucial to maximize the improvement they are able provide, also under consideration that their impact with regard to the vessel’s annual CII compliance should last as long as possible. This can only reasonably be achieved by means of hydrodynamic optimization based on CFD simulations.
CAESES® allows the designers to thoroughly explore the available design space by analyzing many design variants in an efficient automated process. It combines unique parametric geometry modeling and variation capabilities, a comprehensive optimization environment, and flexible interfacing capabilities to connect to external simulation tools (mostly CFD, but also structural analysis, if required). This provides designers with a complete toolset to achieve a truly optimized design, shorten the development time frame, and understand the influence of all involved parameters on the design’s performance.
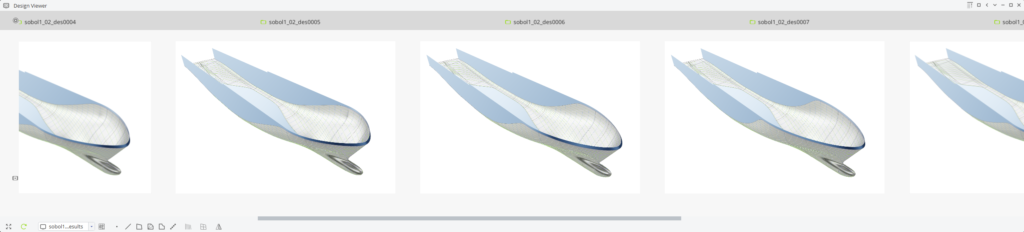
More Information
See this overview to learn more about the capabilities of CAESES® for the design of ship hulls, appendages, and propellers. Contact us to discuss your individual requirements and our solutions in more detail.
Also, take a look at this presentation about how our customer DNV uses CAESES® for the optimization of bulbous bow retrofits.