by Siegfried Wagner
Within the framework of the project “Transitioning to Low Carbon Sea Transport” (TLCSeaT), focusing on the new-build of a sail assisted general cargo and island supply vessel for the Republic of Marshall Islands (RMI), CAESES has been used to create a parametric design and calculation environment that can be used for the evaluation of different design options during the vessel’s concept and early design phases.
The University of Applied Sciences Emden-Leer (HEL) acts as the technical coordinator within the project group and is responsible for the design of this new vessel. The aim of the project is to support RMI in the transitioning process to reach a zero-emission goal in the maritime transport sector. RMI has defined nationally determined climate goals (NDCs) to stepwise reduce emissions from sea transport with the final goal of net zero emissions in 2050.
CAESES was used for different aspects within this initial design phase:
- Generating a parametric, and thus flexible, representation of the vessel concept to investigate and analyze different design options. The flexible 3D model is used as geometric input for further analytical and numerical calculations, as well as for demonstration purposes with project partners.
- Performing analytical calculations using the feature programming environment concerning vessel capacity, stability, and performance predictions for different wind propulsion systems and hydrodynamic layouts.
- Serving as a GUI for CFD calculations with OpenFOAM to investigate flow details of the hydrodynamic layout of the vessel, in order to validate and adapt analytical formulas that are used within the performance prediction procedure.
Concept Design
The concept of this vessel has been developed on the basis of an extensive field research within RMI, carried out in order to define vessel requirements together with the Marshall Islands Shipping Corporation (MISC) in 2020. According to the findings of this field research, a design concept was developed, which has been refined and worked out in detail in a joint effort with the company “Ship Design and Consulting” (SDC), a highly reputable ship design office based in Hamburg.

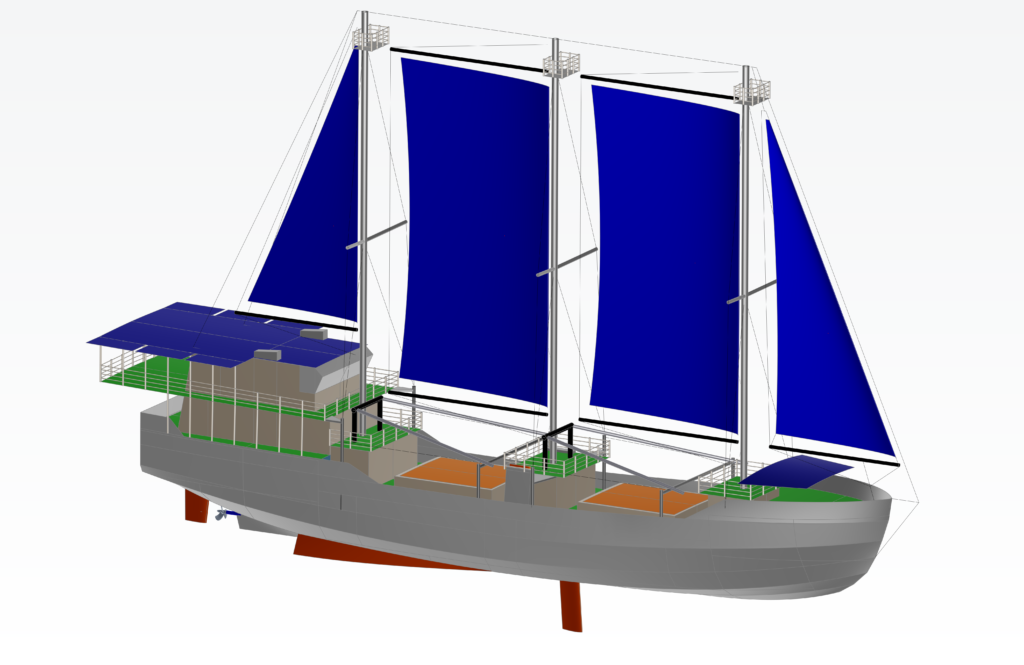
The parametric representation of the model has been used in the early concept phase to investigate and present different design options, and to discuss possible solutions with the project partners in RMI. For this purpose, the layout of the vessel including superstructure, cargo handling system, wind propulsion system, as well as hydrodynamic layout and drivetrain has been integrated into the design.
The parametric approach enabled easily transforming the model based on the discussions with the project partners and thus, new ideas and different solutions could easily be integrated into the design in a fast and efficient way by changing parameters like vessel length, width, height, draft, keel-rake, dead-rise-angle, or the dimensions and positions of superstructure, rigging, and hull appendages.
The feature programming functionality within CAESES was used for fast calculations of areas and volumes for accommodation, tank capacities, and cargo hold volumes, in order to meet the given requirements. All relevant values could be monitored during the design process while the vessel was adapted.
OpenFOAM RANS CFD Simulations
Even though CFD simulations were carried out via a software connection to OpenFOAM, a strong focus was put on the analytical calculation procedure that allows to predict average vessel performance (speed, power demand, and fuel consumption) for a wind assisted commercial vessel. Since the CFD simulations are based on the same geometric input that is used for the analytical computations, a direct comparison of analytical and CFD results for identical flow conditions and hydrodynamic settings could be realized.
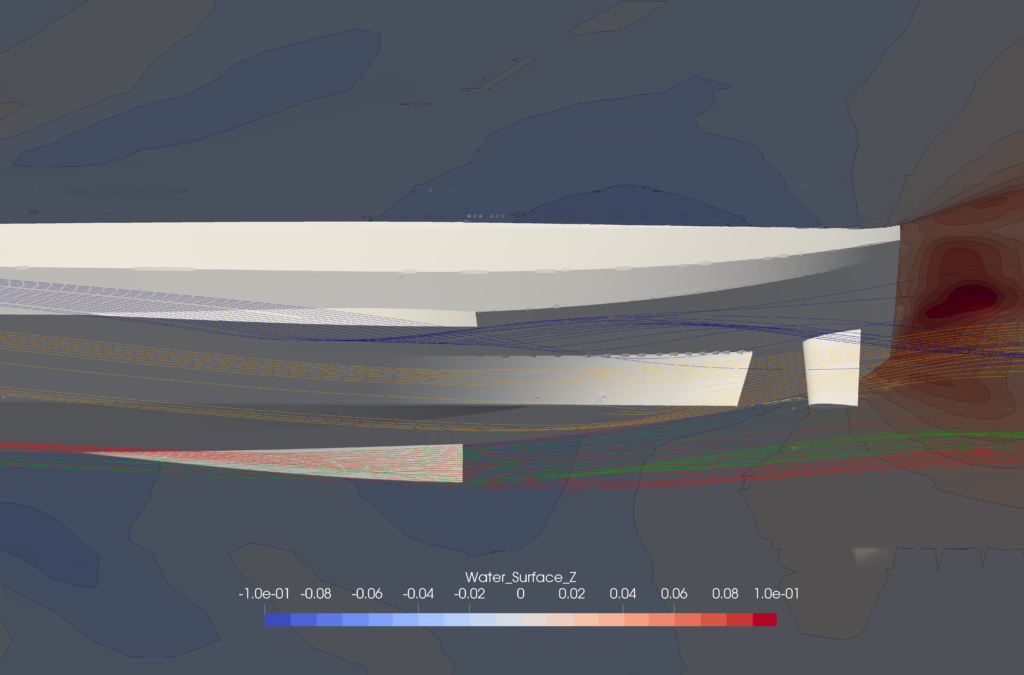
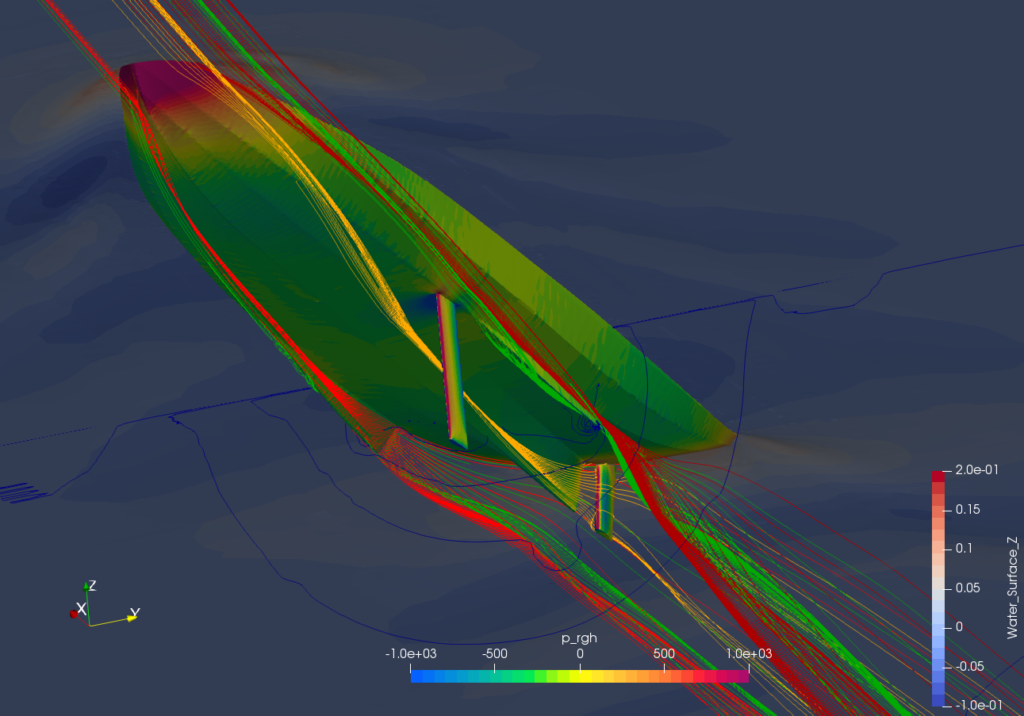
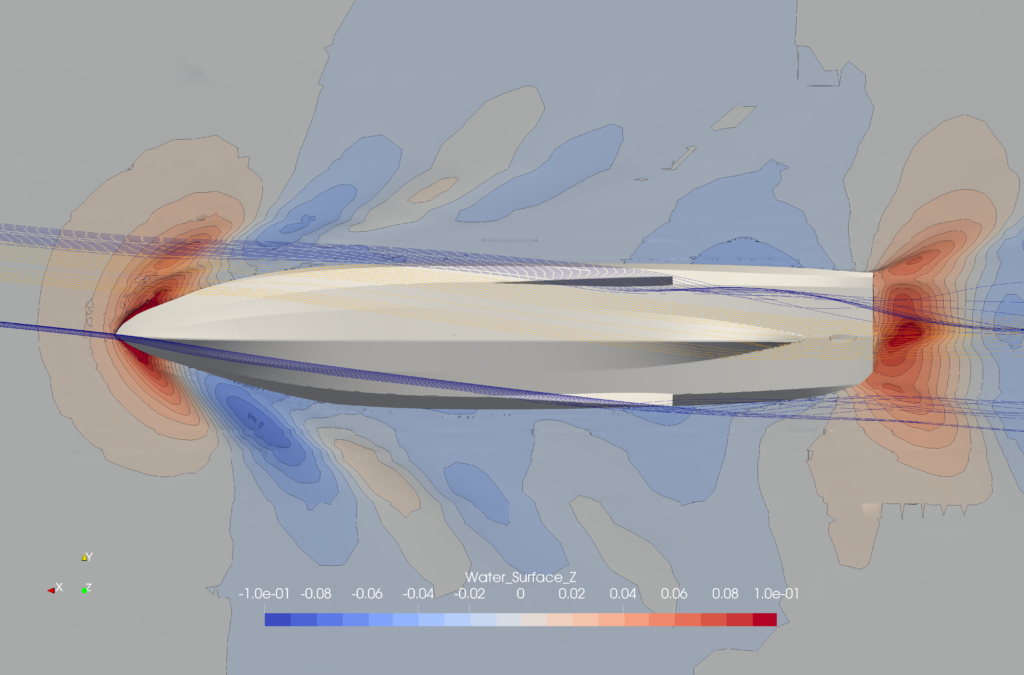
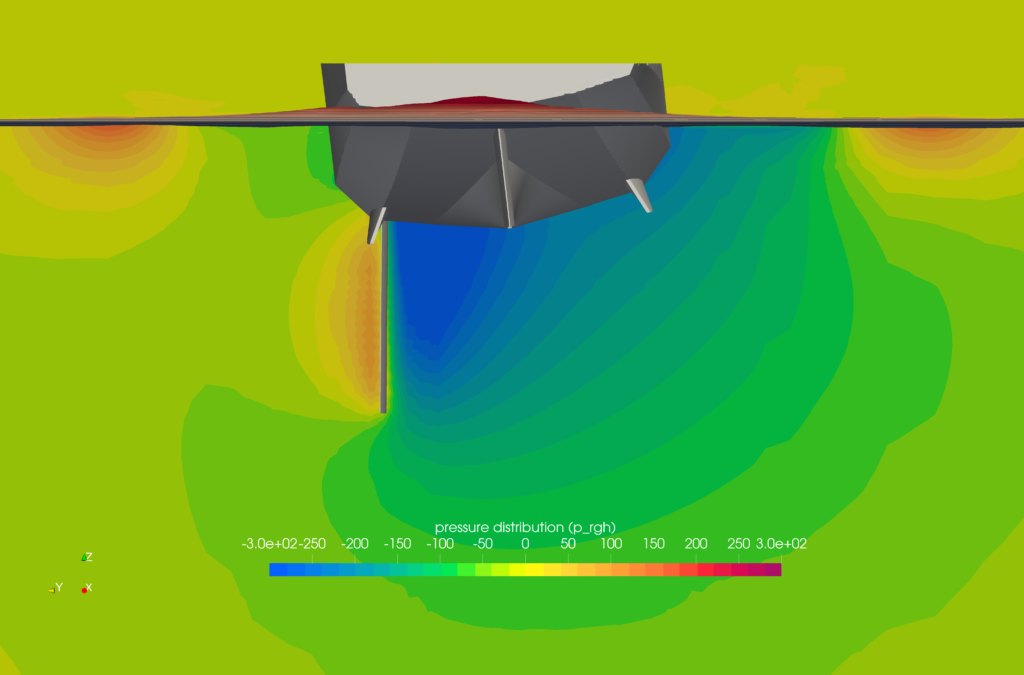
RANS CFD simulations are time consuming and thus not feasible if hundreds of conditions must be calculated to evaluate the benefit of changes made to the design. CFD computations were however used for comparing single flow conditions to evaluate the quality of the analytical formulas used for monitoring the design process.
Performance Prediction
The primary achievement that could be realized is the performance prediction tool, developed in the feature programming environment within CAESES. The main benefit for using CAESES in this context is the direct geometric input from the vessel design that makes it possible to get immediate feedback to any changes made to the model. An analytical calculation concept is especially necessary for vessel performance calculations, where hundreds of equilibrium conditions (equilibrium of aero and hydrodynamic forces and moments) must be calculated in an iterative procedure for each design option that shall be evaluated.
The evaluation procedure starts by collecting all relevant data from the model and then using this data within the feature programming code for the performance calculations. A 4 degree of freedom model has been programmed for combined wind and engine thrust based on analytical formulae on the hydrodynamic side, as well as imported wind tunnel measurements for the representation of the wind propulsion system. The code was able to solve the equation system for the whole wind-spectrum (around 400 equilibrium conditions) within a few minutes.
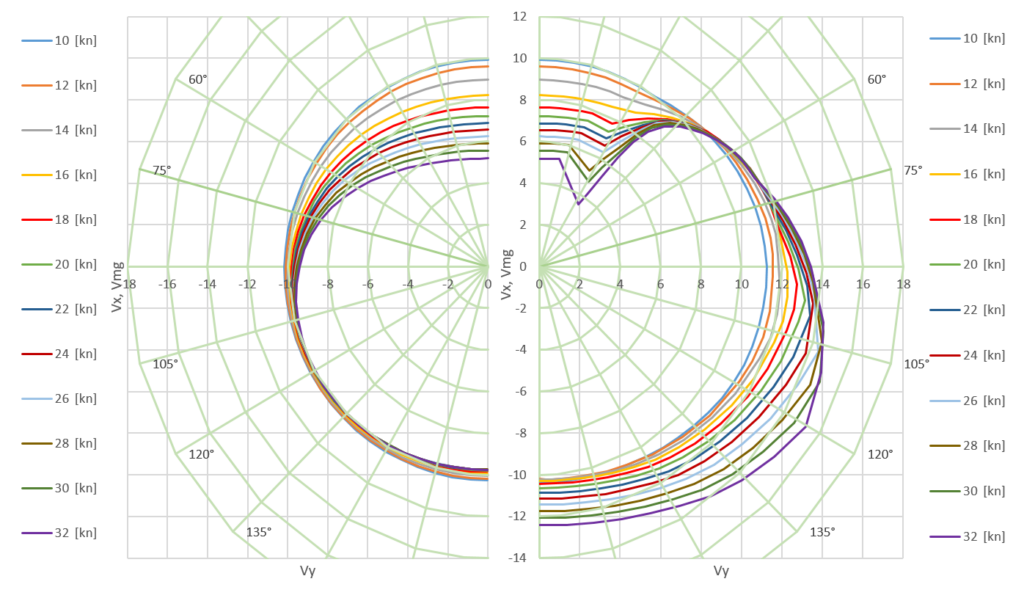
Results
The result of these calculations is a vessel response matrix that yields speed and power demand as a function of wind force and direction. If a specific wind profile (area or trade route dependent) is multiplied with this matrix, average values for vessel speed and power demand can be calculated and used for the determination of average fuel consumption per nautical mile. This final value for fuel consumption per nautical mile has been used to compare and evaluate different design options within the process, thus reducing complex calculation results to the single value of increased or reduced fuel consumption.
Apart from the final value concerning fuel consumption and emissions, the approach allows detailed insights on vessel performance and drivetrain efficiencies. It gives valuable information on the layout and positioning of appendages and helps in the process of optimizing size and orientation of different appendage solutions.
The example displayed in the following diagrams shows the influence of recuperation (i.e., extraction of power from a free milling propeller) on vessel speed and rudder efficiency. The analytical approach realized with CAESES feature programming makes it possible to evaluate the benefit of different measures on the vessel’s performance. For this specific case, the design aim was to optimize the size of the rudder and positioning of the side keels as to not overload the rudder in recuperation mode. Reduced propeller stream velocities lead to increased rudder angles that can become critical if the inflow angle is too close to stall.
Outlook
Further efforts will be made in the future to optimize the performance prediction code in order to make it robust enough for automated optimization procedures within CAESES. Part of this optimization and validation process will be the integration of new maritime testing facilities (towing tank and wind-tunnel) that will complement the existing numerical calculation possibilities at the Maritime Technology Centre at the University of Applied Sciences Emden-Leer.
About the Author
Special thanks to Siegfried Wagner for these insights into the design of wind assisted cargo vessels.
Siegfried Wagner studied naval architecture and ocean engineering and is a research assistant at the University of Applied Sciences Emden-Leer and the Fraunhofer workgroup for Sustainable Maritime Mobility.
Siegfried Wagner
“What I like most about this software is the parametric approach in combination with the feature programming environment that allows me to pick up data from my three-dimensional model directly in the freely definable code. In combination with the optimization algorithms and the software connector, this is a very powerful tool that can speed up the work process enormously and open new doors in the field of CAD and CFD research.”
– Dipl. Ing. Siegfried Wagner – Research assistant at University of Applied Sciences Emden-Leer, Fraunhofer workgroup for Sustainable Maritime Mobility