CAESES® comes with a set of CFD post-processing features, which are mainly used to quickly assess and compare the flow behavior of the generated design candidates. The visualization of 3D streamlines is a standard procedure of CFD engineers to get…
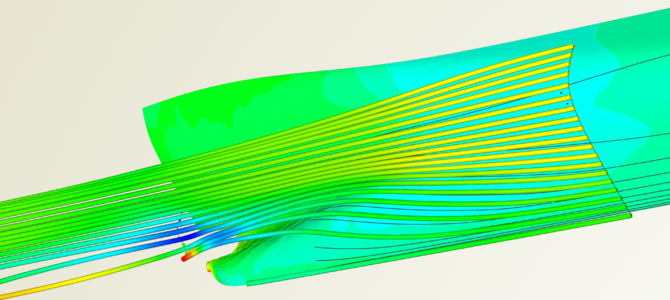
CAESES® comes with a set of CFD post-processing features, which are mainly used to quickly assess and compare the flow behavior of the generated design candidates. The visualization of 3D streamlines is a standard procedure of CFD engineers to get…
Do you design turbomachinery blades in CAESES® and you want to make use of ANSYS TurboGrid for meshing the variable geometry? Then check out the following quick guide which shows you the export procedure. It’s super fast and easy! Such…
Our partner Flow Science recently published an interesting article about the runner system optimization with FLOW-3D Cast and CAESES®. This case study comes with a set of nice and illustrative pictures plus some details about the optimization results. For us,…
For the CFD-driven shape optimization of water pumps with shrouded impellers, it is crucial to have an efficient variable geometry model with a set of relevant parameters (“design variables”). Let’s briefly illustrate and outline the modeling process of a typical…
CAESES allows turbomachinery designers to create efficient parametric geometry for endwall contouring, in order to optimize not only the blades but also the hub surfaces.
Some time ago we had a request from a propeller designer to come up with an easy-to-use parametric geometry model in CAESES® for the Wageningen B-Series. There is a mathematical definition published for setting up such a marine ship propeller…
Here at FRIENDSHIP SYSTEMS, we recently carried out a case study for an automated optimization process based on the shape sensitivities computed by an adjoint CFD solver. The open-source optimization toolkit Dakota by Sandia National Labs, that is integrated in…
For the optimization of flow-exposed products, CAESES® offers a set of strategies that allows users to automate the intelligent design creation process. Design variables are linked to the variable geometry and get controlled by algorithms that are called design engines.…
In the context of different R&D projects over the last few years, we at FRIENDSHIP SYSTEMS have developed and implemented a new method for our product CAESES® that is based on the direct coupling of our efficient CAD parameterization and…
Some time ago, our customer MTU Friedrichshafen (the core entity of Rolls-Royce Power-Systems) approached us with a very interesting request. They design large turbochargers for diesel engines, and they use CAESES® for the design of volutes and other engine components.…