An automated design study was conducted by OMIQ srl on a poppet valve from Danfoss High Pressure Pumps, Denmark. During bench tests the valve was found to exhibit unstable dynamic behavior that was unacceptable. When the valve opened to its maximum displacement (27.5 mm), flow instabilities acted to reduce the pressure forces on the poppet, which resulted in the valve not staying completely open (closing to ~6 mm). These unstable phenomena were verified by transient simulations using SimericsMP®.
To investigate this problem and to improve the design, OMIQ used CAESES® and SimericsMP® in an automated workflow to explore the design space of the valve. Although the valve’s behavior is inherently transient, it was decided to conduct steady-state simulations at the fully-open position with a flow rate of 53 m3/h. This approach was deemed to be valid since the pressure forces are maximum in the fully-open position, and with the added benefit of much faster simulations.
Parametric Model of the Poppet
CAESES® was used to create a parametric model of the poppet described by 4 parameters. The variations were restricted to the underside surfaces of the poppet since there was more freedom to modify those surfaces and high-pressure forces in that region had a large impact on the valve’s behavior. The variations were constrained such that the distance between the poppet and the support in the fully-open position would be maintained.
Optimization
The CAESES® optimization toolkit was used and a Sobol algorithm was selected to conduct a design of experiments (DoE) with 30 designs to make a sweep through the design space. A subsequent local optimization using the T-search method from the best DoE design was used, however, little further improvement was found, thus the best DoE design was considered to be the “optimal” design.
Results
The baseline transient calculation showed that the spring force at the fully-open position is 12.64 N, which indicated that the fluid forces acting on the poppet must be higher than this value for the valve to remain fully open. For structural reasons, the fluid force was confined to a value lower than 17 N, which is the value of the spring force when the valve is in contact with its back support.
The DoE study with 30 designs was successful in uncovering a design that solved the unwanted instability problem. Modifications to the under surfaces of the poppet were effective at reducing flow instabilities that led to the unstable dynamic behavior, causing the valve to partially close. The figure below shows the geometric differences between the baseline and best DoE design.
The following figures show several velocity and pressure contour and vector plots, which depict the differences in the flow field.
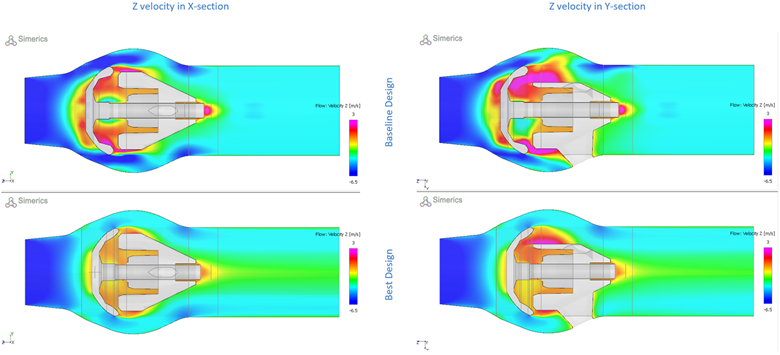
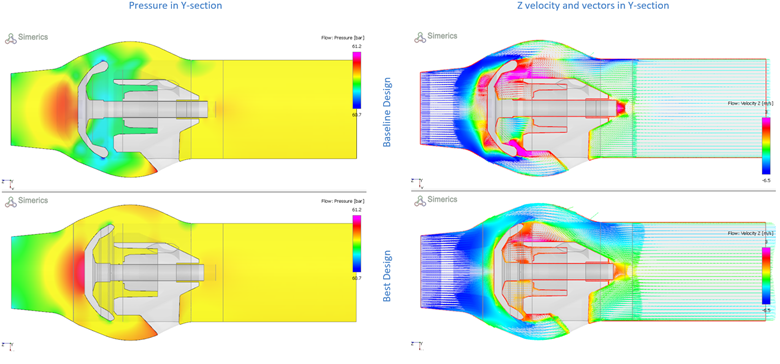
Verification of the Poppet Valve Optimization
To verify the valve’s dynamic behavior was functioning correctly, a transient simulation was run on the best DoE design. Whereas the baseline model opened to 27.5 mm and then closed back, the best DoE design opened to 29 mm in 0.039 s and stayed open. Furthermore, in the fully-open position (and all positions) the maximum spring force was found to be ~13 N, well below the design limit of 17 N.
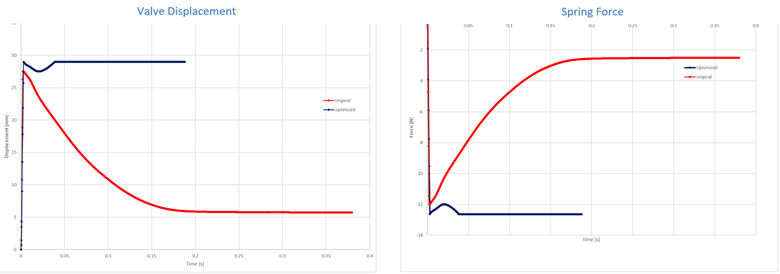
Conclusion
In conclusion, problematic dynamic instabilities in the operation of the baseline poppet valve were effectively solved by setting up an automated workflow with CAESES® and SimericsMP®. A DoE study of 30 designs was run quickly and effectively where design variants were automatically generated by CAESES® and simulated by SimericsMP® in steady-state. The results were verified by follow-up transient flow simulations in SimericsMP® and finally by bench tests at Danfoss HPP.
Mission accomplished! 🙂
Acknowledgement
We would like to thank OMIQ srl (Milan, Italy) for leading this project on the optimization of the poppet valve using CAESES® and SimericsMP®. We would also like to thank Christian Svendsen of Danfoss High Pressure Pumps for his collaboration in this project.
The original case study can be found on OMIQ’s website.