The CAESES ACT app is an ANSYS geometry interface by FRIENDSHIP SYSTEMS that allows CFD engineers to automate the entire geometry generation process, for the purpose of running shape optimization and design studies.
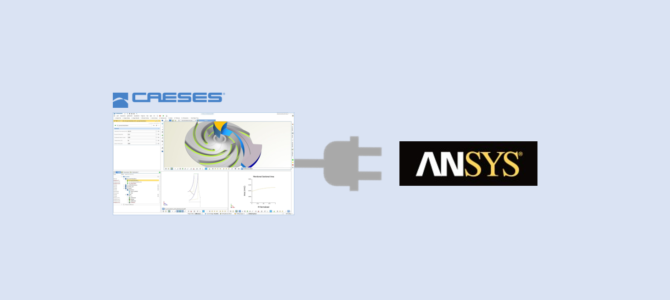
The CAESES ACT app is an ANSYS geometry interface by FRIENDSHIP SYSTEMS that allows CFD engineers to automate the entire geometry generation process, for the purpose of running shape optimization and design studies.
The design of axial fans typically considers the efficiency but also the reduction of the noise emissions. Axial fan noise reduction is a rather huge and complex topic when it comes to all the details, but there are a few simple CAD techniques that you can apply to your standard blade designs, to immediately enhance the fan’s noise level.
When we talk about CFD optimization software, we actually think of a an entirely automated engineering process that covers geometry generation, meshing, simulation and design post-processing. All of these single steps are automated to create a closed optimization loop where, finally, the optimal design candidate(s) emerge from the process, showing optimal results in terms of the product’s flow behavior (e.g. minimum pressure loss, lowest drag, reduced wave resistance, flow homogeneity, robustness for different operating conditions, etc.).
Learn the basic concept of meta surfaces in CAESES, to create advanced parametric sweep surfaces with more controls.
With CAESES version 4.4.2, we introduced a set of new features to automate the CFD software CONVERGE for the purpose of conducting design explorations and shape optimization. This short article gives you an update on the existing CAESES capabilities and their function in the context of using CONVERGE as your CFD software.
In this blog post, we’ll take a quick look into an automated workflow for the fast and flexible design of propeller CAD models that are also suited for automated shape optimization with CFD (Computational Fluid Dynamics).
With CAESES 4.4.2, we’ll introduce a new surface type, the Gordon surface. This surface can be seen as a complementary tool for situations where you would create Coons patches in CAESES. So, what it does is, allowing you to create a surface patch based on a given network of curves. This set of U- and V-curves needs to be ordered for generating the parametric surface.
In the context of gas and steam turbines, the design and optimization of turbine blade cooling structures is a critical task for turbomachinery engineers. The higher temperatures the first turbine stages can endure, the higher thermal efficiency can be realized.…
In this blog post, we have compiled the 10 major steps we typically got through to create parametric models of volutes in CAESES. In some specific situations and with very specific cross sections, we need to use different approaches. But generally the following steps work well. All screenshots and animations are taken from within the CAESES GUI. Hope you’ll like it!
FRIENDSHIP SYSTEMS AG strives to reduce energy consumption and emissions by supporting its customers in improving their products, most notably ships as well as turbomachinery and engine components. Therefore, we have taken a look at the question how much CO2-emissions…