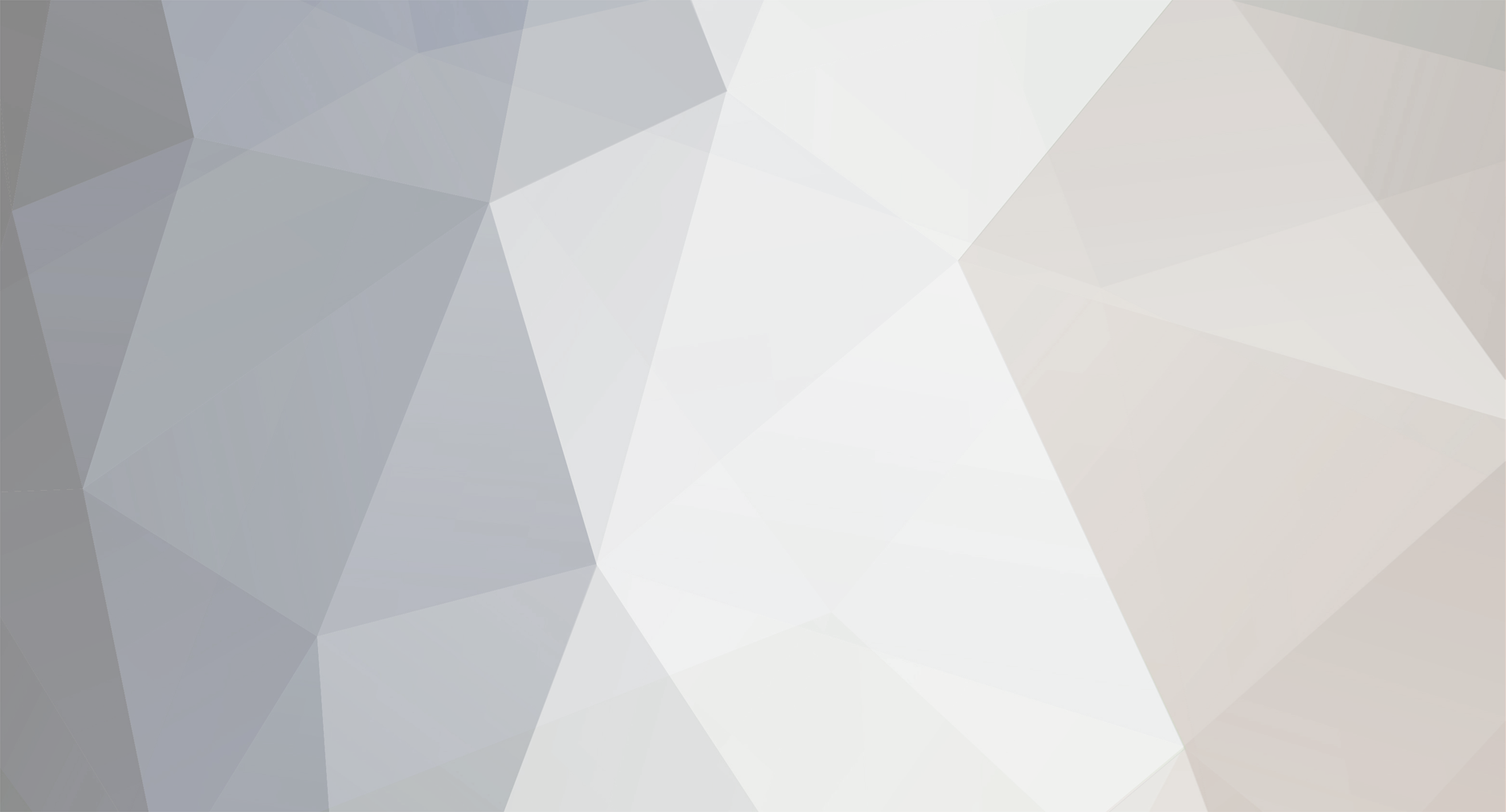
Mr. Heinrich von Zadow
Moderators-
Content Count
223 -
Joined
-
Last visited
-
Days Won
12
Mr. Heinrich von Zadow last won the day on April 8
Mr. Heinrich von Zadow had the most liked content!
Community Reputation
12 GoodAbout Mr. Heinrich von Zadow

-
Rank
Moderator
Profile Information
-
Gender
Not Telling
Recent Profile Visitors
-
Mr. Heinrich von Zadow started following Modified CSV files cannot be used as result pools, Surrogate Assisted Optimization, Fuction rand() generates not-really-random values and and 7 others
-
Surrogate Assisted Optimization
Mr. Heinrich von Zadow replied to adrian.portillo.juan's topic in General Modeling
Hi Adrian, but can't you just open the project in CAESES and adjust the boundaries of your LHS sampling algorithm in the GUI? You can then still run the project in batch mode for the generation of the designs... Or do you do the sampling (i.e. LHS) through a method within your python setup? I'm asking, because CAESES does also provide LHS sampling... Also, instead of sampling a large design space and then another one in a second iteration, you could use the adaptive sampling method within CAESES. This will automatically start with a LHS and then switch to an adaptive mode based on uncertainty quantification or other criteria. You can check the documentation for an example on how to run CAESES in batch mode. Cheers Heinrich -
Fuction rand() generates not-really-random values
Mr. Heinrich von Zadow replied to Sody's topic in Feature Programming
Hi Sody, I think one should be careful when using the rand() function in a persistent feature. It seems to remember a fixed seed somehow. If you do not create a persistant feature instance in your project, but rather just transiently execute the definition repeatedly it should behave as expected. Cheers, Heinrich -
ffd FFD or deltashift Command question
Mr. Heinrich von Zadow replied to Graychen's topic in General Modeling
Hi there, this looks like you are shifting control points too much (or maybe you are shifting them smoothly but accidentally left out a group of points that is just outside the range thereby folding the polygon in an unwanted manner). Try looking at the control polygon to get a better understanding of what went wrong. In addition, I highly recommend to update to the latest release. Cheers, Heinrich -
Hi Adam, that looks promising already. When combining everything, you need to distinguish between boolean operations and simply adding sources. I went through your model and corrected a few things -- mostly adding the domain faces one-by-one using individual "add sources" operations. While doing so, I colored each operation so that your inlet/outlet/periodics, etc are colored reliably. I did the same for the blade and extruded and closed it to obtain a closed solid (you don't want any open/red edges and your final BRep should be closed > you can tell it is closed from it's icon being filled with grey color). Then there is only one boolean operation: substracting the closed blade from the closed domain. Since the blade and tip are already colored, the colors will "imprint" onto your domain during that operation. Hope this helps. Cheers, Heinrich FAN4_HvZ.cdbc
-
Hi Adam, take a look at BReps -- they are the way to go when combining, uniting, substracting, etc. various parts of your geometry. For boudary conditions you can make use of colors (their names) which can be applied robustly even when topologiacal changes occur in the model during shape variation. You should be able to find everything to get started within the help menu of CAESES. Cheers, Heinrich
-
CAESES outputs NAPA-format hull line file
Mr. Heinrich von Zadow replied to Mr. Chang Xie's topic in Ideas and Suggestions
Hi there, a few users have successfully implemented such features with varying degree of complexity. If you are familiar with NAPA definitions you can easily write a custom export in CAESES. However, there is no solution readily available in CAESES. Kind regards, Heinrich -
Hi Yuvraj, if everything else is set up correctly, you should be able to abort the CFD run and just take a look at the 'finaldata' file that is written by Dakota. This contains the predicted optimal design (or Pareto set, if multi-objective) and the predicted evaluations. Kind regards, Heinrich
-
CAESES to ANSYS Workbench Boundary Colors Issue
Mr. Heinrich von Zadow replied to Praveen's topic in Software Connections
Hi Praveen, thanks for the update, much apprechiated. Indeed, surfaces do not propagate their colors, BReps do. Cheers, Heinrich -
CAESES to ANSYS Workbench Boundary Colors Issue
Mr. Heinrich von Zadow replied to Praveen's topic in Software Connections
Hi Preveen, not sure if the problem still persists on your side? Have you chacked the documentation on boundary coloring/naming in CAESES? It should give plenty of information. Generally, there are no limitations on what colors can be exported ot not (except from export formats that do not support coloring). The name exported will always be the name of the color unless you specify a custom export name for that color. Cheers, Heinrich -
CAESES to ANSYS Workbench Boundary Colors Issue
Mr. Heinrich von Zadow replied to Praveen's topic in Software Connections
Hi Praveen, how did you label/color the subsequent BRep faces? Have you tried to export and import back to CAESES to verify the colors are there? Cheers, Heinrich -
Difference between i=i+1 and i+=1
Mr. Heinrich von Zadow replied to Piero Favero's topic in Feature Programming
Hi Piero, that should definitely work. My best guess is that the problem arises somewhere else in you feature. Could you post the complete Feature definition? Cheers, HEinrich -
Problem Connecting to OpenFoam
Mr. Heinrich von Zadow replied to gratschiller's topic in Software Connections
Hi WX, have you been able to resolve the issue in the meantime? Does it start the allrun script from within CAESES and have you set up any result values or files such that CAESES would know what to look for and when to consider the computation finished? Cheers, Heinrich -
Modified CSV files cannot be used as result pools
Mr. Heinrich von Zadow replied to Yukai's topic in Variation & Optimization
Hi Yukai, you can import the csv file via "Import Result Pool" in the optimization workspace to use it as a database for subsequent optimizations. Cheers, Heinrich -
Hi Alexis, if you choose to use existing result pools, designs that have been simulated before will not be simulated again. Instead, the old results will be linked. Cheers, Heinrich