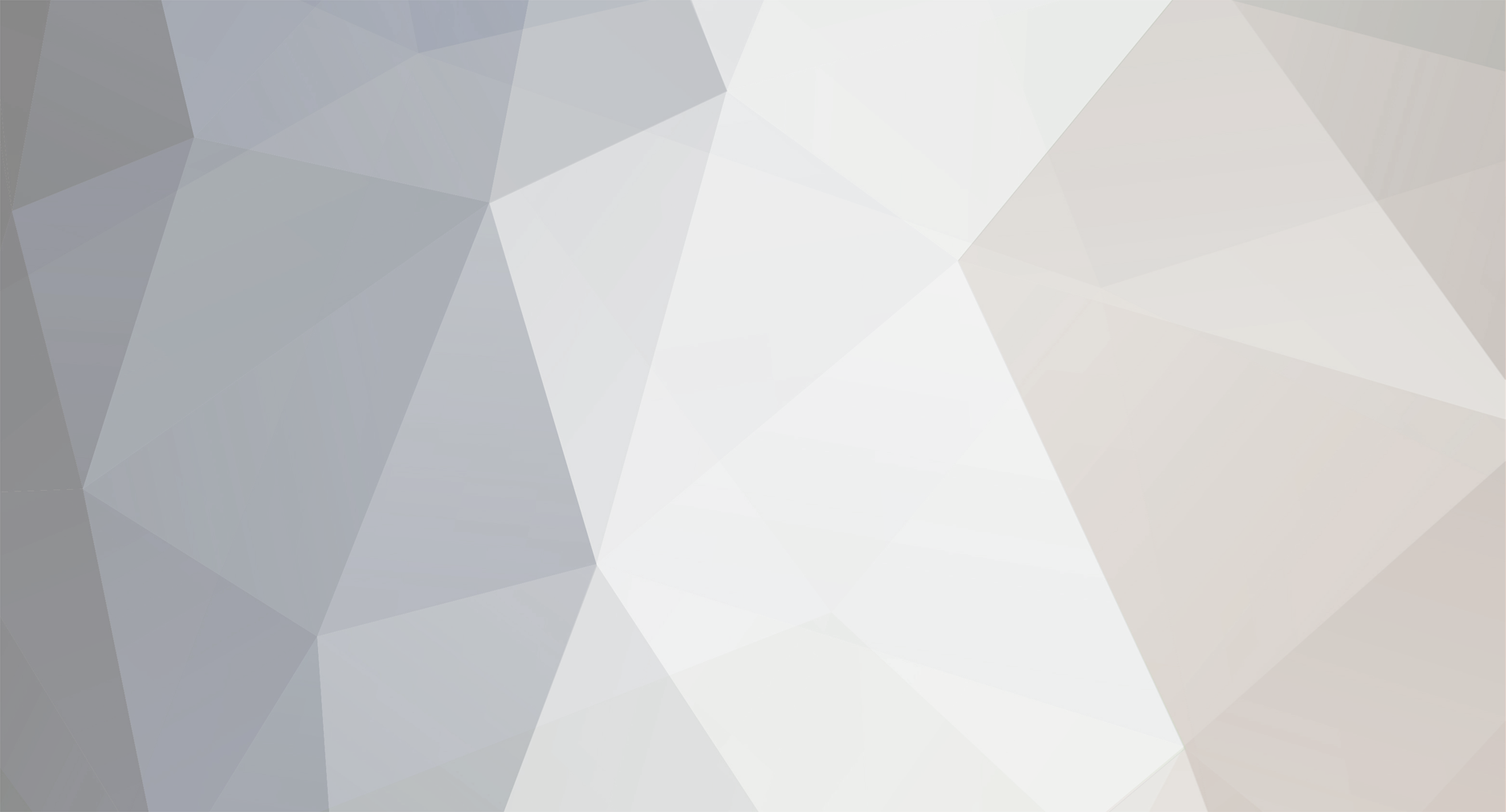
GK_YD
Members-
Content Count
10 -
Joined
-
Last visited
Community Reputation
0 NeutralAbout GK_YD
-
Rank
Member
Recent Profile Visitors
The recent visitors block is disabled and is not being shown to other users.
-
Trimesh Post-Processing Issues (for .stl STAR-CMM+)
GK_YD replied to GK_YD's topic in Post-Processing
Dear Mattia, Firstly, I'd like to thank you for your input on the subject. The BRep post processing really helped a lot, regarding the tesselation. On your first question I don't have yet an answer, however when I tried to import and the .step form I faced the same issues. However, I'd like to experiment a bit more with the post-processing settings and file forms in order to have a clear answer to your question, which is a question of mine too. I'll reply on the matter upon further info. Thanks a lot again. Cheers, George -
GK_YD started following Surface Discrepancies on Hull, Trimesh Post-Processing Issues (for .stl STAR-CMM+), Brep or Surface trimming issues and and 2 others
-
Dear all, I've created a trimesh (FTrimesh) from a BRep hull geometry, which I'd like to export in an form in order to import it into STAR-CMM+, while also later I'd like to run an hull optimization run. The first issue is that while the Open Edges option is active, in the 3DView it shows none open edges, while simultaneously it shows that there is 1 Open Edges at the Info panel. This leads to an number of issues while trying setting up the STAR-CMM+ simulation, since it cannot create volume meshes. The next question is how can I increase the density of the tessellated geometry, in particular the number of triangles on the created mesh? Is there a way to modify the triangles in other ways, such as isoscales triangles, or similar options? Thank you very much for your time and consideration. George. Tecopt_v1.cdbc
-
Hi and thank you for checking up the model. I checked on the proposed solution and also found the problem you've mentioned via another way of trimming the excess surface/brep. Regarding the No. of sections, I think I've left them 2000 by mistake, on the process of checking the potential of the surface and how it was displayed. Now I've returned both values (Interpolated points & Number of Sections) to 10 & 100 respectively, as of a previous suggestion of yours (on another post of mine). I'm attaching the new file below, while I'd like to ask how should I close the bow upper section of the hull (till the X-plane) in a fair way, by assuring continuity in curvature (attaching relative photo as well)? Thank you again for your time. Best, George TestSWAN_v3.cdbc
- 2 replies
-
- hull design
- brep
-
(and 3 more)
Tagged with:
-
Spray rails parametric modeling on fast monohull design
GK_YD replied to GK_YD's topic in General Modeling
Dear Mr. Claus, Thank you very much for your input and suggestions. I took my time in order to study your solution and especially how easily, though how effectively you parametrize the model. Thank you again for you input on my topic. Best regards, George- 2 replies
-
- hull design
- fast monohull
-
(and 2 more)
Tagged with:
-
Dear all, I'm having some issues trimming the Brep or Surface either with curves, surfaces or Breps. My intention is to parametrize the end of the Brep or Surface in order to end at the transom (x=0) of the hull, while at the same it follows the step. I manage only to trim the surface (04_UpperSectionSurface) first on the principal plane (X=0) first and then trim the Brep (06_Step|Upper_Section_Brep) on the step geometry, however this ends with some discrepancies on the final Brep, due to the initial trimming of the 04_UpperSectionSurface. I'm attaching a few screenshots of the area, while also the model. Could you please advise upon the matter? Thanks a lot. Best regards, George TestSWAN_v2.cdbc
- 2 replies
-
- hull design
- brep
-
(and 3 more)
Tagged with:
-
Dear all, Currently working on a fast monohull parametric design and I'm in the process of adding some spray rails to the hull, as the images attached below. I'd like to ask if their is any efficient way to parametrize such geometry at the hull surface and/or if anyone had worked on a similar project and maybe could share some details and insights on the topic? Attached you may find my project while also some photos of spray rails geometries Thank you in advance for your time. Best regards, George TestSWAN_v2.cdbc
- 2 replies
-
- hull design
- fast monohull
-
(and 2 more)
Tagged with:
-
Dear all, I'm having some issues trimming the Brep or Surface either with curves, surfaces or Breps. My intention is to parametrize the end of the Brep or Surface in order to end at the transom (x=0) of the hull. I'm attaching a few screenshots of the area, while also the model. Could you please advise upon the matter? Thanks a lot. Best regards, George TestSWAN_v2.cdbc
-
- hull design
- brep
-
(and 1 more)
Tagged with:
-
@Mr. Claus AbtThank you very much for the information and guidance, I'll check the definitions of the curves and points again and revert respectively.
-
@Mr. Claus Abt Thank you very much for your comment. The initial generation method of MetaSurface was skinning, and still on some values of the design variables (mostly Bot angle 1 & Bot Curve Weight) there were some discrepancies, while the sections, waterlines and buttocks showed smooth transition. Do you know if this by any mean could be a visual issue and not an actual surface one?
-
Hello everyone, Currently working on my thesis project for optimization of a planning craft (approx. 9m). I've modeled the hull of the craft with a MetaSurface and at about the center of the hull there are some surface discrepancies, which are becoming visually more clear while experimenting with some of the design variables. Could you please advise on the matter? Is this a visual issue, if no which are the process options in order to maintain the same magnitude of variation for the most of design variables? Moreover, please advise on the optimization of the Parameters & Design Variables having in mind the planning craft principles. Koula_Design.cdbc